Aiming for proactive quality assurance for the future of our business
Yui Morimoto
Quality Assurance Section, Naoshima Smelter & Refinery, Metals Company
Quality Assurance Section, Naoshima Smelter & Refinery, Metals Company
Quality initiatives shift from “reactive” to “proactive”
The Naoshima Smelter & Refinery supplies basic materials for industrial society through copper and precious metal smelting and recycling operations. I have been a member of the Quality Assurance Section for two years and am responsible for two main types of work. One is to check each delivery lot to see if the specifications of the products to be shipped meet the customer’s requirements, and issue an inspection certificate. The other is to act as the secretariat of the QMS (Quality Management System), managing and guiding each department to comply with the rules based on the requirements of ISO9001.
One of the important missions of the QMS secretariat is to maintain ISO certification. While we make various adjustments within the plant prior to the regular audits, there is no time to take a breather after passing the certification audits. From the next day, we must start the PDCA cycle again to enhance the QMS. Through monthly meetings with the quality managers of each department, the QMS secretariat discusses and shares information on QMS-related operational and business problems and solutions in the course of daily activities. As part of our duties, we also propose reviews of rules related to quality management, which sometimes develop into reviews of the entire operational structure of the plant. Because this work involves the entire organization, it is necessary to understand the roles of each department and seek rules that are easy for everyone to follow. It can be a tough job, but I find it very rewarding.
You may think of quality assurance as a “reactive” job where we continue to do exactly what has been decided.
Indeed, the traditional role of quality assurance is to ensure that non- conforming products are not shipped. However, this is now changing. The Mitsubishi Materials Group as a whole is now taking a “proactive” approach to quality assurance, which is to avoid producing non-conforming products. I, too, would like to continue to implement the PDCA cycle and develop the Naoshima Smelter & Refinery’s QMS into one that is worthy of being called “proactive” quality.
One of the important missions of the QMS secretariat is to maintain ISO certification. While we make various adjustments within the plant prior to the regular audits, there is no time to take a breather after passing the certification audits. From the next day, we must start the PDCA cycle again to enhance the QMS. Through monthly meetings with the quality managers of each department, the QMS secretariat discusses and shares information on QMS-related operational and business problems and solutions in the course of daily activities. As part of our duties, we also propose reviews of rules related to quality management, which sometimes develop into reviews of the entire operational structure of the plant. Because this work involves the entire organization, it is necessary to understand the roles of each department and seek rules that are easy for everyone to follow. It can be a tough job, but I find it very rewarding.
You may think of quality assurance as a “reactive” job where we continue to do exactly what has been decided.
Indeed, the traditional role of quality assurance is to ensure that non- conforming products are not shipped. However, this is now changing. The Mitsubishi Materials Group as a whole is now taking a “proactive” approach to quality assurance, which is to avoid producing non-conforming products. I, too, would like to continue to implement the PDCA cycle and develop the Naoshima Smelter & Refinery’s QMS into one that is worthy of being called “proactive” quality.
Self-study toward becoming an indispensable employee
Since being assigned to the Quality Assurance Section, I have been studying the specialized knowledge required for my work from the ground up. I also tried to obtain QC Kentei (Quality Control Certification) Grade 2, which QC managers are required to obtain. The first time, I failed by a whisker. The second time, I gave up taking the test because the ship I was supposed to take could not leave Naoshima Island due to dense fog. The third time, I finally passed the test. Later, I also obtained a certification to become a quality control manager for JIS (Japanese Industrial Standards) products. My knowledge and skills have improved, and I feel my work is going well. Currently, I am trying to obtain certification as a general certified measurer. The Naoshima Smelter & Refinery is designated as an appropriate measurement control business place, where in-house certified measurers perform periodic inspections of meters used for transactions and verifications. The use of properly controlled meters is a prerequisite for accurate quality assessment, and certified measurers are essential for maintaining quality because they keep meters in proper condition. However, the Naoshima Smelter & Refinery has only a minimum number of certified measurers, so I decided to pursue the certification. I would like to become an indispensable employee by taking charge of essential tasks for the company.
Continuing to take on challenges toward the future of the Naoshima Smelter & Refinery
I am proud of the Naoshima Smelter & Refinery. For more than 100 years since its establishment, it has made full use of raw materials, even commercializing the by-products of copper and precious metal smelting. Furthermore, it has contributed to the realization of a sustainable society by achieving zero-emission recycling, in which 100% of the recycled raw materials are reused.
That is why we want to develop the company so that the Naoshima Smelter & Refinery can exist for the next century. As an employee, I would like to evolve myself and be part of the driving force to develop the company by taking on new challenges without being afraid of changes.
That is why we want to develop the company so that the Naoshima Smelter & Refinery can exist for the next century. As an employee, I would like to evolve myself and be part of the driving force to develop the company by taking on new challenges without being afraid of changes.
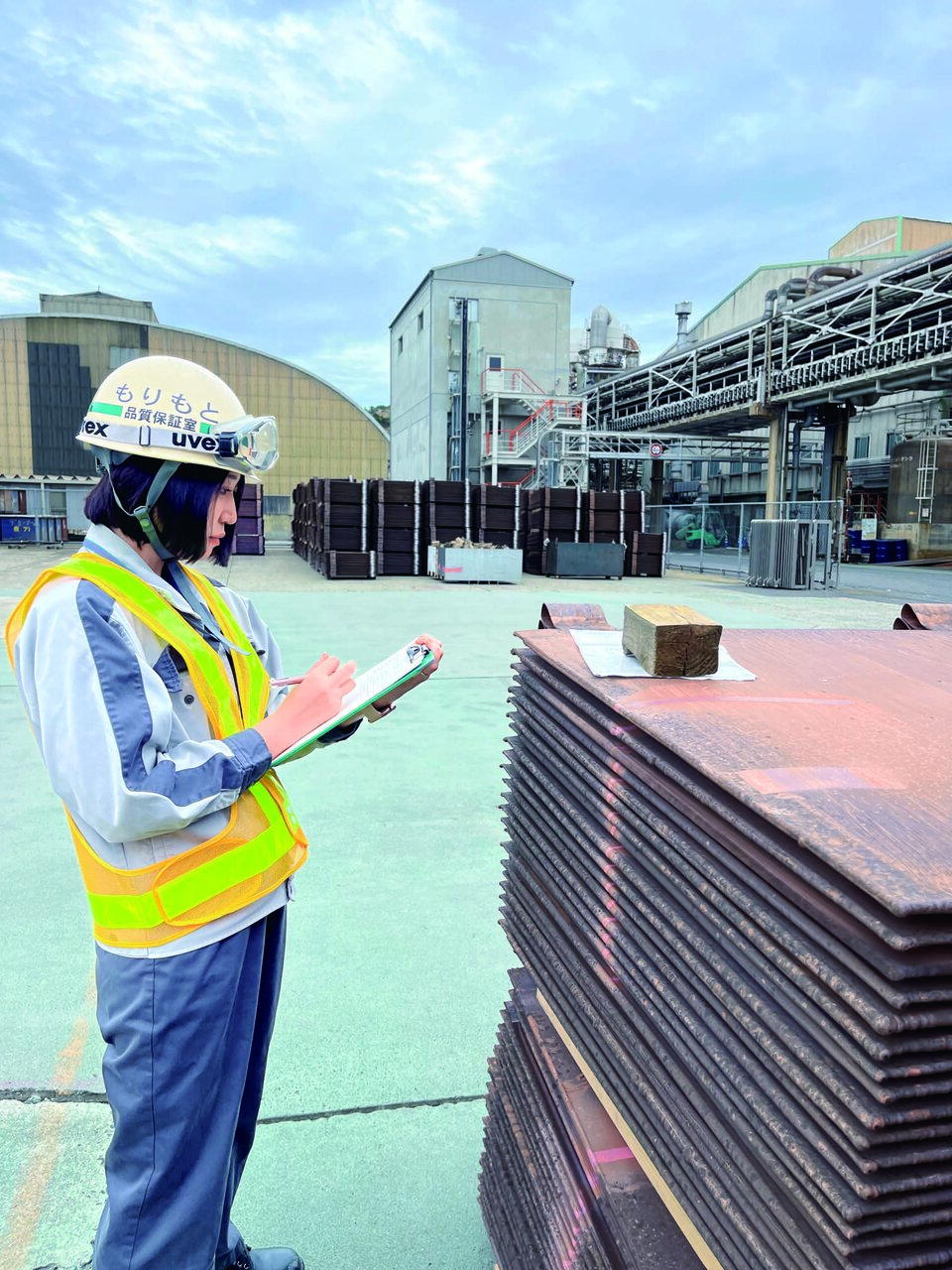
To deepen my understanding of each department’s role and products, I review QC process charts and standard operating procedures and visit actual work sites.