Special Feature : Using the Power of Technology to Create the Future Vol.3
Combination of strength and heat resistance of the world’s highest standard
The Path to the Development of MOFC-HR (Mitsubishi Oxygen Free Copper - Heat Resistance)
In 2021, Mitsubishi Materials developed MOFC-HR (Mitsubishi Oxygen Free Copper – Heat Resistance), a new oxygen free copper with the world’s highest standard of strength and heat resistance. This material has characteristics which will advance the electrification of automobiles and the spread of next-generation energy, contributing to a sustainable society. We want to share with you the strenuous efforts of the people that went into the development of this new material.
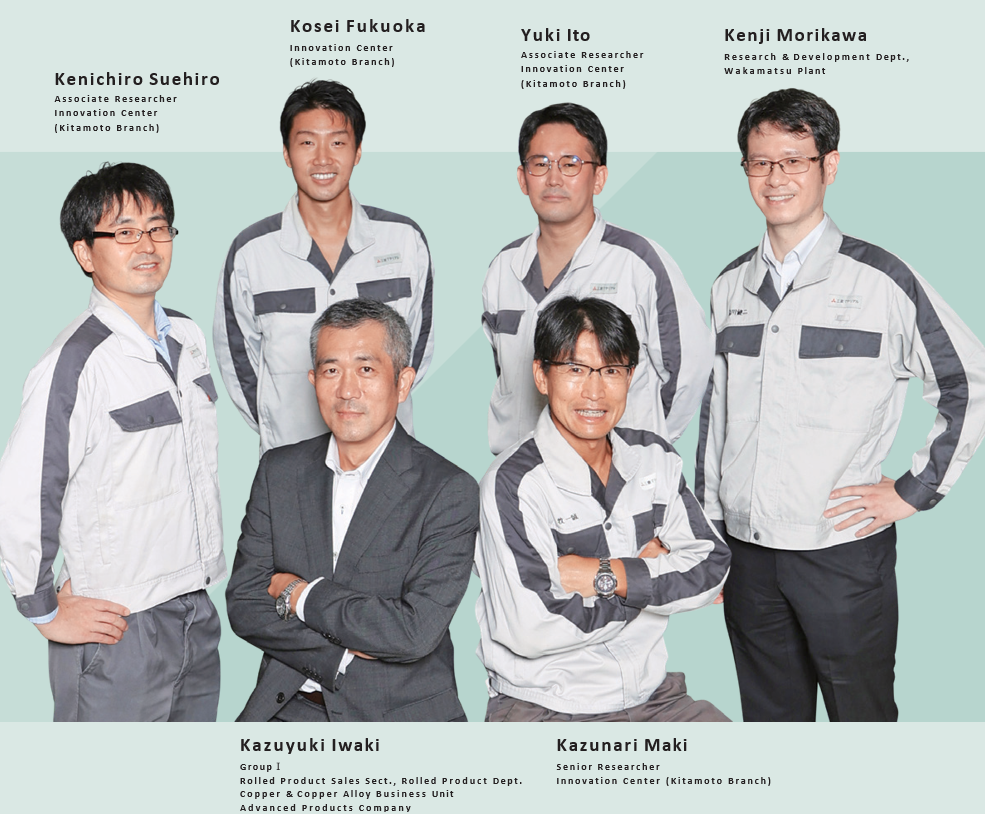
Copper materials evolve in the age of electrif ication
Mitsubishi Materials has developed an integrated Copper and Copper Alloy Business, from copper smelting to wrought copper products. For many years, the company has been developing a variety of copper products to satisfy customers’ needs, and particularly excels in the development and manufacturing technologies of oxygen free copper and its alloys.
In recent years, the electrification of automobiles and the spread of next- generation energy has led to the demand for materials of electrical components that can handle large electric currents and have high heat dissipation capability. For this reason, the use of oxygen free copper, the copper material with the highest electrical conductivity and heat conductivity, is rapidly spreading.
However, when pursuing higher reliability or functionality, a problem with existing oxygen free copper was its insufficient strength and heat resistance. “Those engaged in research and development for a company have a mission to release technologies into the world and to create things that help people. We at Mitsubishi Materials must continue to evolve our specialty oxygen free copper to fulfill the customers’ needs,” says research and development supervisor Maki.
In recent years, the electrification of automobiles and the spread of next- generation energy has led to the demand for materials of electrical components that can handle large electric currents and have high heat dissipation capability. For this reason, the use of oxygen free copper, the copper material with the highest electrical conductivity and heat conductivity, is rapidly spreading.
However, when pursuing higher reliability or functionality, a problem with existing oxygen free copper was its insufficient strength and heat resistance. “Those engaged in research and development for a company have a mission to release technologies into the world and to create things that help people. We at Mitsubishi Materials must continue to evolve our specialty oxygen free copper to fulfill the customers’ needs,” says research and development supervisor Maki.
Exploring the possibilities without fear of failure
Five years ago, at the Innovation Center Kitamoto Branch where research and development of metal materials is performed, Associate Researcher Ito’s team was exploring the possibilities of oxygen free copper. “It was believed that the electrical and heat conductivity, which are the strong points of oxygen free copper, were a trade-off for strength and heat resistance. However, customers desired something that had both high electrical conductivity and strength, and not making this happen would hinder the advancement of electrification. To meet their expectations, we tested various compositions through trial and error without fear of failure, and we discovered an interesting phenomenon where an increase in strength did not decrease electrical conductivity as much as we had anticipated. As a researcher, it was a very rewarding moment.” Don’t be afraid of failure. Mitsubishi Materials Innovation Center has an environment where, during the basic research stage, researchers are free to explore possibilities without worrying about the outcome. This development was successful due to this environment.
Mr. Fukuoka was responsible for taking the seeds of discovery from Mr. Ito’s basic research and
brushing them up for productization. “As we made adjustments to the characteristic parameters to optimize the performance, I became more and more convinced with the potential of this material. I would get excited just thinking about the kinds of equipment this oxygen free copper would be used in after overcoming its weaknesses.
There is no doubt MOFC-HR will have an impact on manufacturing.”
Following lab verification, it was finally time for trial production at Wakamatsu Plant. Initially, there was a variation in the performance, and we went back and forth between trial production and lab verification. Mr. Morikawa of Wakamatsu Plant reflects on this period: “It was not an easy task to reproduce the characteristics we discovered in the lab on mass production machines and to establish a process that achieved the specifications that would meet the requirements of our customers. I became keenly aware of the difficulty of launching a new product that had characteristics of the highest standard in the world. But now, I feel lucky to have been part of the process. I want to make MOFC-HR the new standard for oxygen free copper.”
Mr. Fukuoka was responsible for taking the seeds of discovery from Mr. Ito’s basic research and
brushing them up for productization. “As we made adjustments to the characteristic parameters to optimize the performance, I became more and more convinced with the potential of this material. I would get excited just thinking about the kinds of equipment this oxygen free copper would be used in after overcoming its weaknesses.
There is no doubt MOFC-HR will have an impact on manufacturing.”
Following lab verification, it was finally time for trial production at Wakamatsu Plant. Initially, there was a variation in the performance, and we went back and forth between trial production and lab verification. Mr. Morikawa of Wakamatsu Plant reflects on this period: “It was not an easy task to reproduce the characteristics we discovered in the lab on mass production machines and to establish a process that achieved the specifications that would meet the requirements of our customers. I became keenly aware of the difficulty of launching a new product that had characteristics of the highest standard in the world. But now, I feel lucky to have been part of the process. I want to make MOFC-HR the new standard for oxygen free copper.”
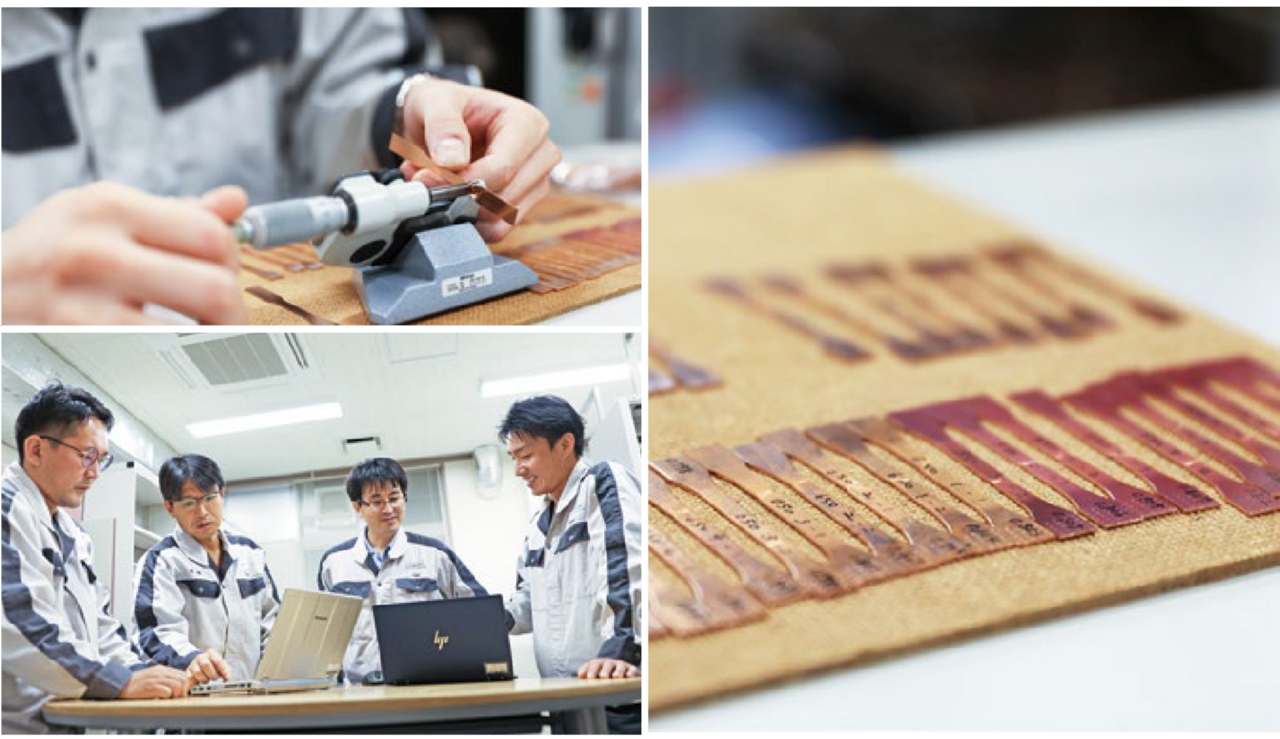
Those engaged in research and development for a company have a mission to release technologies into the world and to create things that help people.
Dialogue inside and outside the company speeds up innovation
Project Manager Suehiro determined the success of this project would not have been possible without the teamwork from both inside and outside the company. “Our company has a flat organization, and this atmosphere allows everyone to freely express their opinions of how to reach the goal without worrying about superior or subordinate relations. Team strengths allowed ideas to spread, and it made for a speedy progress. The process didn’t only take place in the company; we also received many customer inputs from the development stage onward. I believe all of us coming together as one team to meet the needs of the world is what enabled us to create a new product with the capacity of meeting the world’s highest standard. Mr. Iwaki of sales, who was responsible for keeping everyone updated on customer needs, shared the same opinion. “With Innovation Center, Wakamatsu Plant, and the sales division coming together as one, we were able to hear the voices of many customers, helping us to develop a material that matched their needs.
One customer has already assessed MOFC-HR and has highly praised the balance of its superior electrical conductivity and strength, which is its greatest advantage. If the material is strong, there is also the merit of being able to downsize the thickness of the sheet, cutting material costs. I will continue to connect customers with our company so that this material is adopted.”
One customer has already assessed MOFC-HR and has highly praised the balance of its superior electrical conductivity and strength, which is its greatest advantage. If the material is strong, there is also the merit of being able to downsize the thickness of the sheet, cutting material costs. I will continue to connect customers with our company so that this material is adopted.”
A material that is useful to the world and changes the future
After the MOFC-HR press release went public in September 2021, many customers reached out to us with their opinions. With the electrification of our society, there is a high expectation for high strength, high heat resistance oxygen free copper for use in many applications such as high voltage terminals for automobiles, bus bar modules, charging connectors, relay sockets, battery tab leads, power modules, lead frames, heat sinks, and so on. The project team members share a common desire: to create a material that would be useful to the world. They all voiced in chorus that unless the material is actually used, creates value for society, or protects the future of the earth, it has no meaning. In order to meet the needs of the world, Mitsubishi Materials’ research and development team will continue to endlessly take on new challenges.
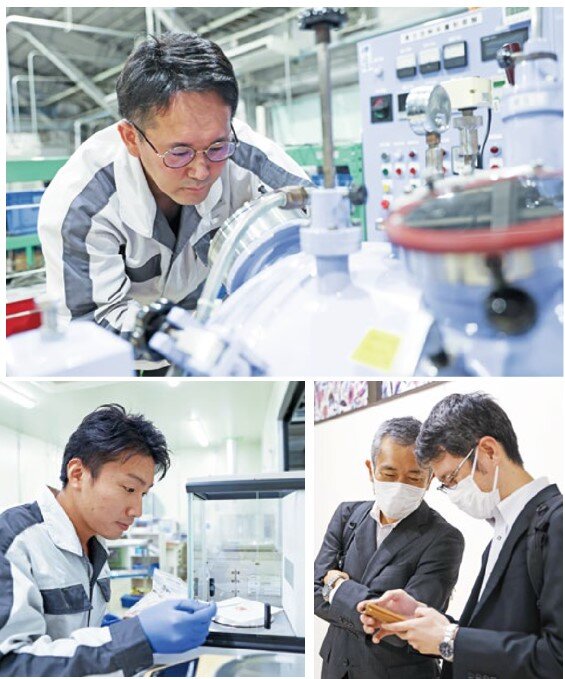
The project team members share a common desire: to create a material that would be useful to the world.