Special Feature : Delivering to the world the material of possibilities - TUNGSTEN Vol.3
Collect It, Convert It, and Expand Possibilities.
The Possibilities of Collaboration of Mitsubishi Materials Group
In this section, we focus on three key areas: “Collect It,” “Convert It,” and “Expand Possibilities,” highlighting the people involved in the circulation of tungsten resources and their intriguing initiatives.
Collect
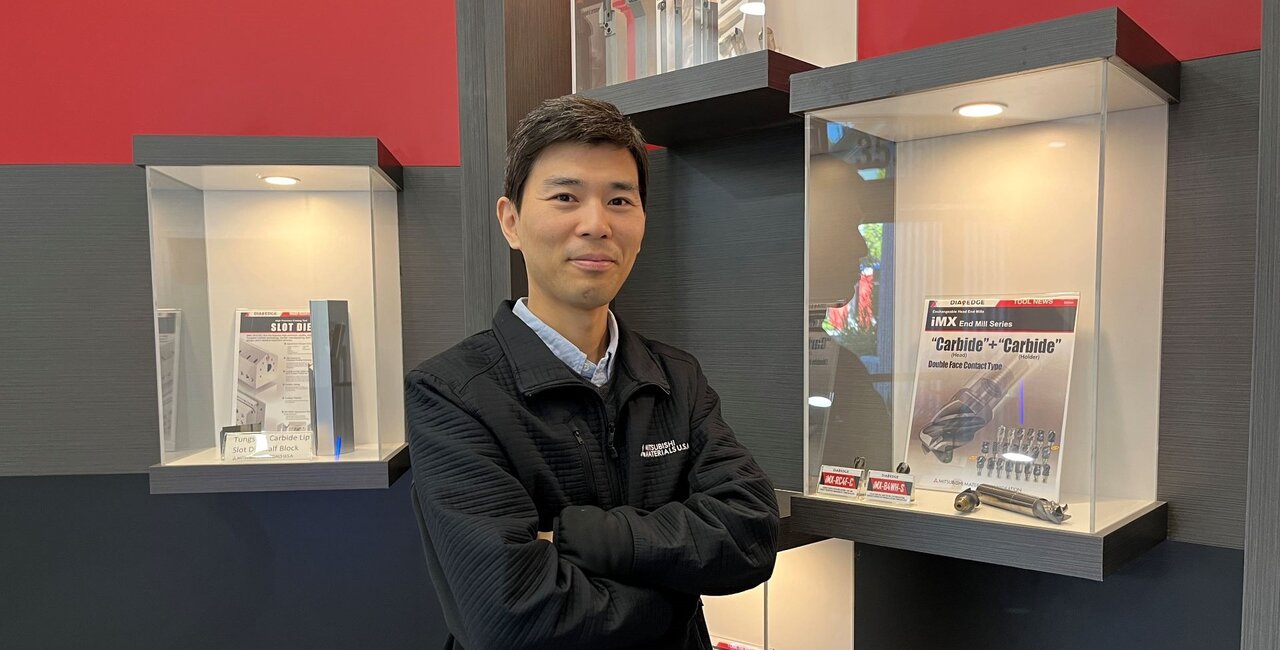
Mitsubishi Materials U.S.A. Corporation
International Procurement Manager
Nobuyoshi Shibazaki
Joined Mitsubishi Materials in 2013 and has consistently handled procurement. After being seconded to the former MMC Superalloy
Corporation (previously the Okegawa Plant), he moved to the Procurement & Logistics Department, and in 2021, was transferred to Mitsubishi Materials U.S.A. Corpo- ration. Currently, he is responsible for procuring carbide scrap in the Americas.
Fostering a healthy competitive environment helps enhance scrap quality
To ensure a stable supply of tungsten, a recycling system is essential. Mitsubishi Materials Group has established a resource circulation system where it globally collects carbide scrap, which contains tungsten, and turns it into tungsten powder anew.
Mitsubishi Materials U.S.A. Corporation (MMUS), where I work, sells Mitsubishi Materials Group’s cutting tools, rock tools, wear resistant tools, and electronic materials in North America, and also procures tungsten scrap. However, “procuring” does not mean that we directly collect items from customers. Instead, scrap dealers collect and clean metal scrap, which contains various metals, and select tungsten scrap among them. MMUS’s role in our Group’s resource circulation system is to buy tungsten scrap from scrap dealers, supply it to tungsten powder manufacturers we partner with, and have it turned into oxidized tungsten, which is a raw material for tungsten powder.
In these processes, I am primarily responsible for purchasing scrap. Since scrap prices fluctuate daily, I inquire about monthly market conditions with our regular scrap dealers to identify optimal prices. While also considering factors like quality, share allocation, and future demand forecasts, I select suppliers. Even if I don’t close a deal, I make it a point to explain the reasons why. I believe this communication encourages scrap dealers to review their prices and improve scrap quality, fostering a healthy competitive market environment. I also aim to build trust with scrap dealers through this communication.
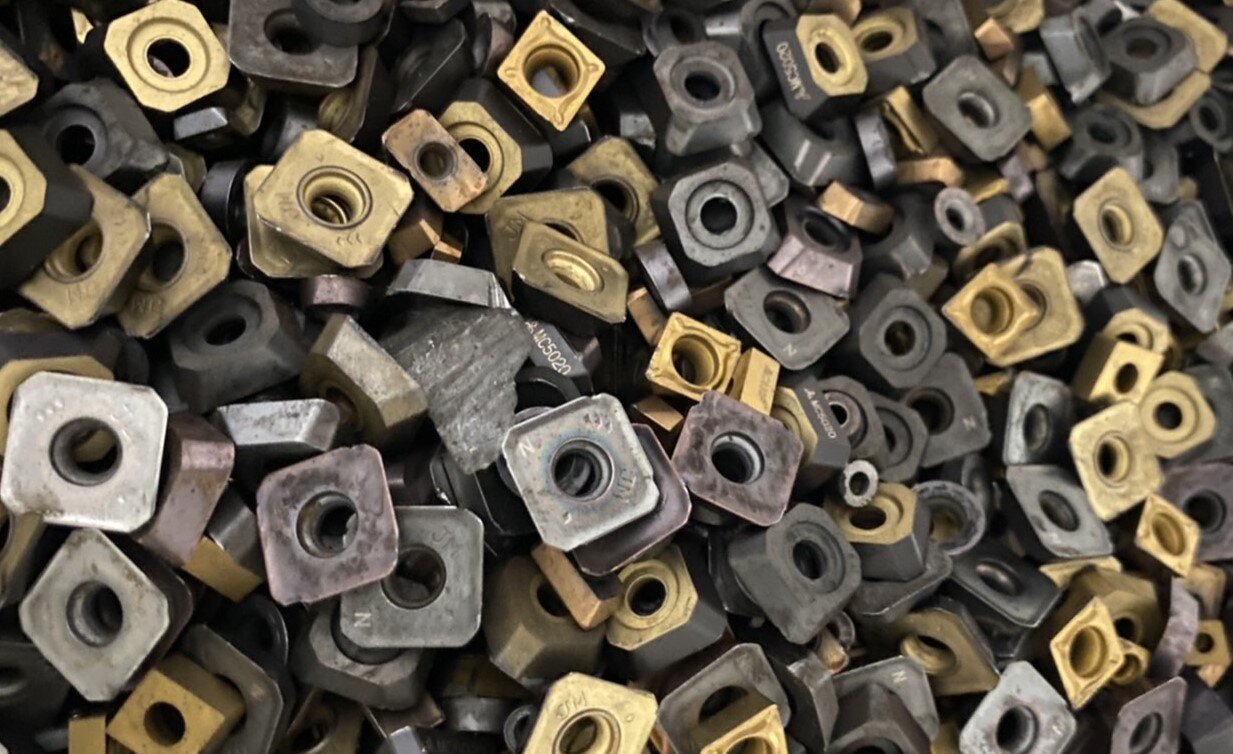
Building face-to-face relationships based on sincerity and trust to invite business opportunities
This is why I focus on building face-to-face relationships with scrap dealers. While there are US companies involved in global tungsten recycling, like ours, only a limited number of scrap dealers can select, analyze, and manage the quality of scarp on a certain scale. To become the preferred partner, we need to establish stronger relationships of trust with scrap dealers than our competitors have. Even in the United States, personal relationships and sincerity still matter in business, so I regularly visit scrap dealers and prioritize face-to-face communication. Our network of scrap dealers varies, from those we’ve worked with for just a few years to those with whom we’ve had a partnership for over a decade. To maintain these long-term relationships, I always value sincerity.
Through these efforts, I hope to earn trust and, ultimately, contribute to in- creasing the volume of scrap collection.
Aiming even higher, with over 80% of the materials used in carbide tool products being recycled
To this end, in May 2024, Mitsubishi Materials Group reached an agreement to acquire all shares of H.C. Starck, a leading tungsten product manufacturer with over 100 years of history. As a result, our Group now has tungsten business operations in four major markets: Japan, Europe, North America, and China. The acquisition of H.C. Starck, with its top-class tungsten recycling capabilities, can strengthen our recycling operations and increase the volume of scrap we can collect. Additionally, welcoming H.C. Starck into our Group enhances trust with scrap dealers, helping to stimulate transactions.
By turning changes in the business environment into opportunities, we aim to further increase the volume of scrap collection. Currently, our Group is strengthening its collection efforts across the Americas, including Mexico and Brazil, in addition to the United States. Looking ahead, we will also strive to expand scrap collection in Europe.
Currently, tungsten scrap procured in North America is transformed into tungsten powder at Japan New Metals Co., Ltd. However, my ultimate goal—or even dream—is to establish a tungsten circulation system completed within the Americas. Beyond these challenges, I aim to contribute to further enhancing our Group’s tungsten recycling capabilities and, with an even higher target, ensure that over 80% of the materials used in carbide tool products are recycled.
Convert It into Resources
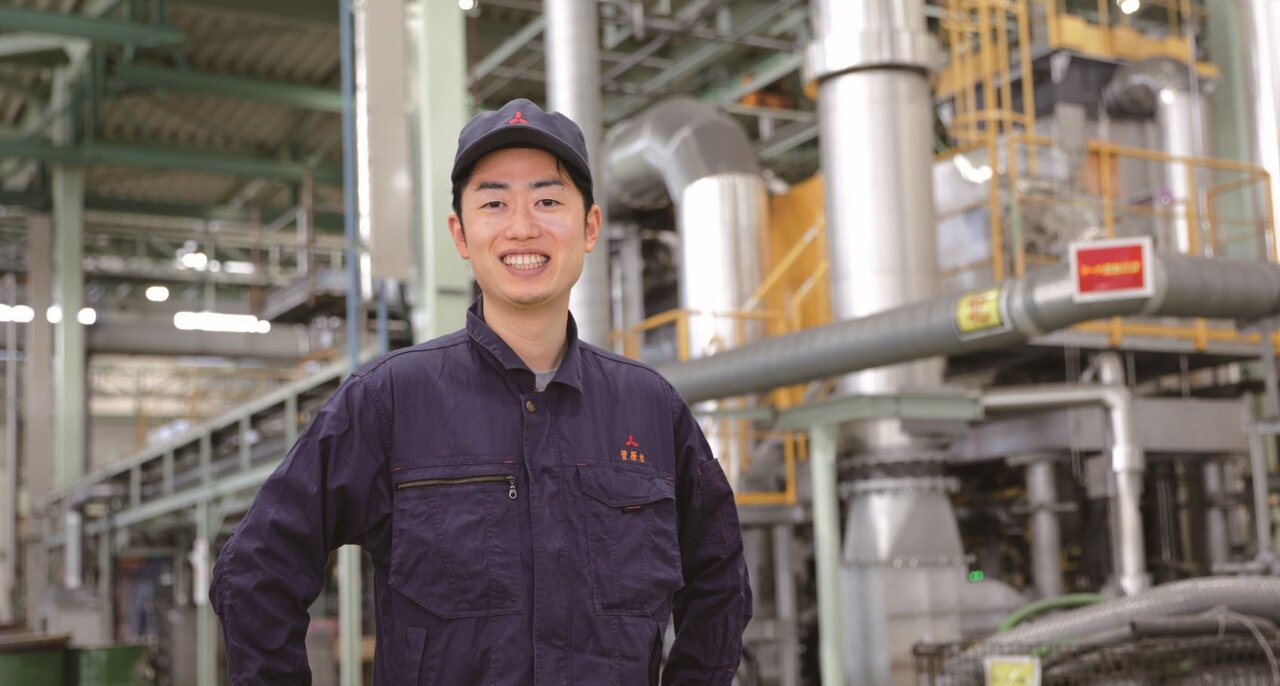
Yuto Sugawara
Manufacturing Group Akita Plant
Japan New Metals Co., Ltd.
Joined Japan New Metals in 2018. After a secondment to the Innovation Center of Mitsubishi Materials, he started working at the Akita Plant. Currently, he conducts internal and external inspections and also engages in joint research with universities to develop new recycling processes.
Leveraging years of experience in operations and expertise to achieve optimal recycling processes
Through these processes, tungsten powder products (WO3, W, and WC) are manufactured. One of Akita Plant’s strengths is its expertise in recycling, hydrometallurgy, and dry processing technologies, which enable us to handle all types of scrap.
The challenge in recycling lies in putting together various types of scrap to make a consistent output. The difficulty of processing depends on the type of scrap. Our company leverages expertise gained over years of operation to conduct recycling, hydrometallurgy, and dry processing, ensuring a stable output of high-quality tungsten powder, regardless of the scrap type. This success is driven by a combination of highly skilled operators and process managers who can make flexible decisions.
Additionally, collaborating with H.C. Starck allows me to envision a future of expanding our business globally, which I find highly significant. Technical collaboration enables us to complement weaknesses and hone strengths together, ultimately leading to the joint development of new recycling processes that extend beyond the capabilities of both companies’ technologies. I am excited about these future possibilities.
Aspiring to contribute to a stable supply through the development of new technologies
There are certain types of scrap that we do not accept due to profitability concerns. As scrap collection expands, it is expected that these inquires will increase. To handle these scraps at a low cost, we will need to develop new recycling processes. In addition to optimizing existing technologies, we will proactively focus on developing new ones, thereby driving change and contributing to a stable supply of tungsten.
Expand Possibilities
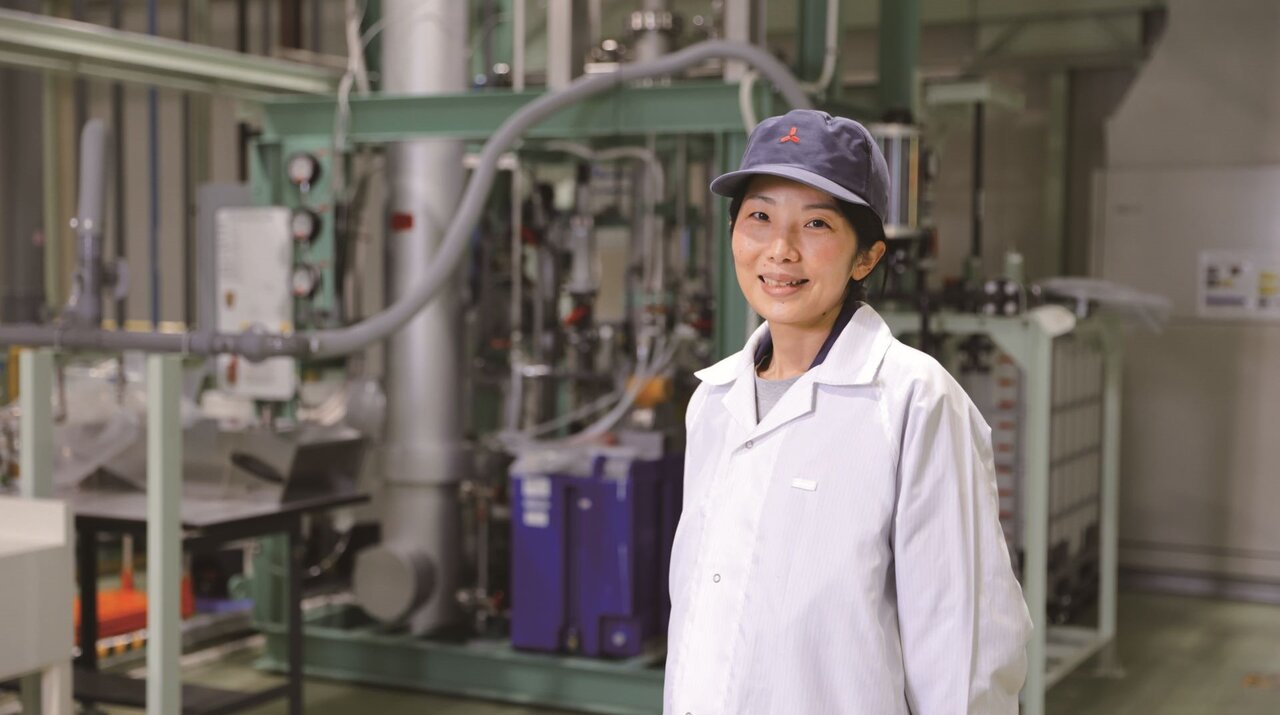
Yuko Kato
Manufacturing Group Akita Plant
Japan New Metals Co., Ltd.
Joined Japan New Metals in 2004 and has primarily handled analysis work. In 2018, she joined the Manufacturing Group. Currently, she follows up on the progress of each theme as the subeader and is particularly responsible for themes related to tungsten hydrometallurgy.
Aiming for recycling technology capable of handling all types of scrap
Expanding the possibilities of tungsten recycling will require the technology to leverage even scrap with unexpected impurities and those that are difficult to handle. While we have encountered various cases in our track record and are capable of handling most of them, we need to further advance this technology by adapting to changes over time. The key to this is the hydrometallurgy process. As this requires identifying optimal conditions, such as which chemicals to add and how much to use to remove impurities, we would like to establish methods by utilizing the know-how and expertise we have cultivated to date.
I am also addressing environmental measures for tungsten hydrometallurgy. Since this technology handles ammonia (NH3), the Akita Plant faces an issue with high nitrogen (N) emissions. Excessive nitrogen can impact water quality. To be environmentally friendly and sustainably expand our business, we aim to collect and reuse ammonia nitrogen.
Refining technology together as a Group to promote resource circulation
Our role is to promote and strengthen tungsten recycling to support a stable supply of tungsten. To this end, we will enhance existing technologies to handle more challenging scrap. I aim to apply my past experience in analysis and daily takeaways to future work.
Furthermore, by refining recycling technology together as a Group, including H.C. Starck, I would like us to promote the circulation of tungsten re- sources and drive business expansion.