With everyone’s satisfaction comes a workplace where each individual shines
Hideyuki Fujimoto
Precision Silicon Products Group Manufacturing Unit No. 2, Manufacturing Div., Sanda Plant
Precision Silicon Products Group Manufacturing Unit No. 2, Manufacturing Div., Sanda Plant
The key to improve productivity is to “create a workplace in which each individual can fully exercise their power”
Smartphones, vehicles, medical equipment, and much more connect to the internet in this era of IoT. As a matter of fact, Mitsubishi Materials’ products are being used in a wide range of manufactured IoT equipment. The creators of those products are the Mitsubishi Materials Group members who work in Japan and at international locations spanning over 31 countries and regions. Recently, however, the business environment surrounding us is changing rapidly with a shortage of workers due to population decline and soaring raw material prices because of the difficult global situation. During this time of change, Mitsubishi Materials is working to improve productivity at each of its manufacturing sites under its corporate philosophy, “For People, Society and the Earth.” So, how will we do that?
After thinking back on the 15 years I have worked at the Sanda Plant, I think the answer is to “create a workplace in which each individual can fully exercise their power.”
After thinking back on the 15 years I have worked at the Sanda Plant, I think the answer is to “create a workplace in which each individual can fully exercise their power.”
Satisfaction in understanding will motivate your next action
“What do you think is the root cause?”
This question was asked to me by an older coworker after I had just joined the company, and it remains in my mind as an important lesson. I was a general high school graduate who knew almost nothing about the world of manufacturing when I joined the company. Whenever a problem occurred, I would just wait for directions from senior staff. However, that question made me start to try to figure out a situation myself before reporting it to others. Thanks to that, I started to understand workflow and act of my own initiative.
I am now the leader of a seven-person team, and whenever a younger member asks me a question, I make sure not to give them the answer right away. I first ask them the same question my coworker asked me and then we think of the answer together. The first step to growing is thinking on your own, and the satisfaction that comes from understanding will become the motiva- tion for your next action.
This question was asked to me by an older coworker after I had just joined the company, and it remains in my mind as an important lesson. I was a general high school graduate who knew almost nothing about the world of manufacturing when I joined the company. Whenever a problem occurred, I would just wait for directions from senior staff. However, that question made me start to try to figure out a situation myself before reporting it to others. Thanks to that, I started to understand workflow and act of my own initiative.
I am now the leader of a seven-person team, and whenever a younger member asks me a question, I make sure not to give them the answer right away. I first ask them the same question my coworker asked me and then we think of the answer together. The first step to growing is thinking on your own, and the satisfaction that comes from understanding will become the motiva- tion for your next action.
What we focused on was the feeling that we were making the work more efficient with our own hands
From April 2022, our company is making efforts to raise productivity and strengthen our supply chain as part of our strategy of differentiating manufacturing capabilities of each plant. In the manufacturing process of silicon components used for semiconductor manufacturing equipment, I am currently in charge of the engineering process of raw materials, and I am taking initiative to improve the productivity of this process.
The first step I took was filming the work of three of my team members so we could visually see their processes. After that, the entire team sat down to watch the video, voice their opinions, such as “This is the second time they did this, but it only needs to be done once,” and “If we slack on this cleaning process, it could lead to equipment malfunctions, so please be careful,” and look for where we could improve.
The most important thing to me during this process was that every team member felt they themselves were improving daily work efficiency. While working to make these changes, some people were hesitant to change the way we had always done things, but we also had many people say, “I feel less confused about work now,” which made me feel this work was worth it.
I will continue helping people connect through these activities. I also hope to pass on to the next generation the culture that is the foundation of this work, “create a workplace in which each individual can fully exercise their power, together.”
The first step I took was filming the work of three of my team members so we could visually see their processes. After that, the entire team sat down to watch the video, voice their opinions, such as “This is the second time they did this, but it only needs to be done once,” and “If we slack on this cleaning process, it could lead to equipment malfunctions, so please be careful,” and look for where we could improve.
The most important thing to me during this process was that every team member felt they themselves were improving daily work efficiency. While working to make these changes, some people were hesitant to change the way we had always done things, but we also had many people say, “I feel less confused about work now,” which made me feel this work was worth it.
I will continue helping people connect through these activities. I also hope to pass on to the next generation the culture that is the foundation of this work, “create a workplace in which each individual can fully exercise their power, together.”
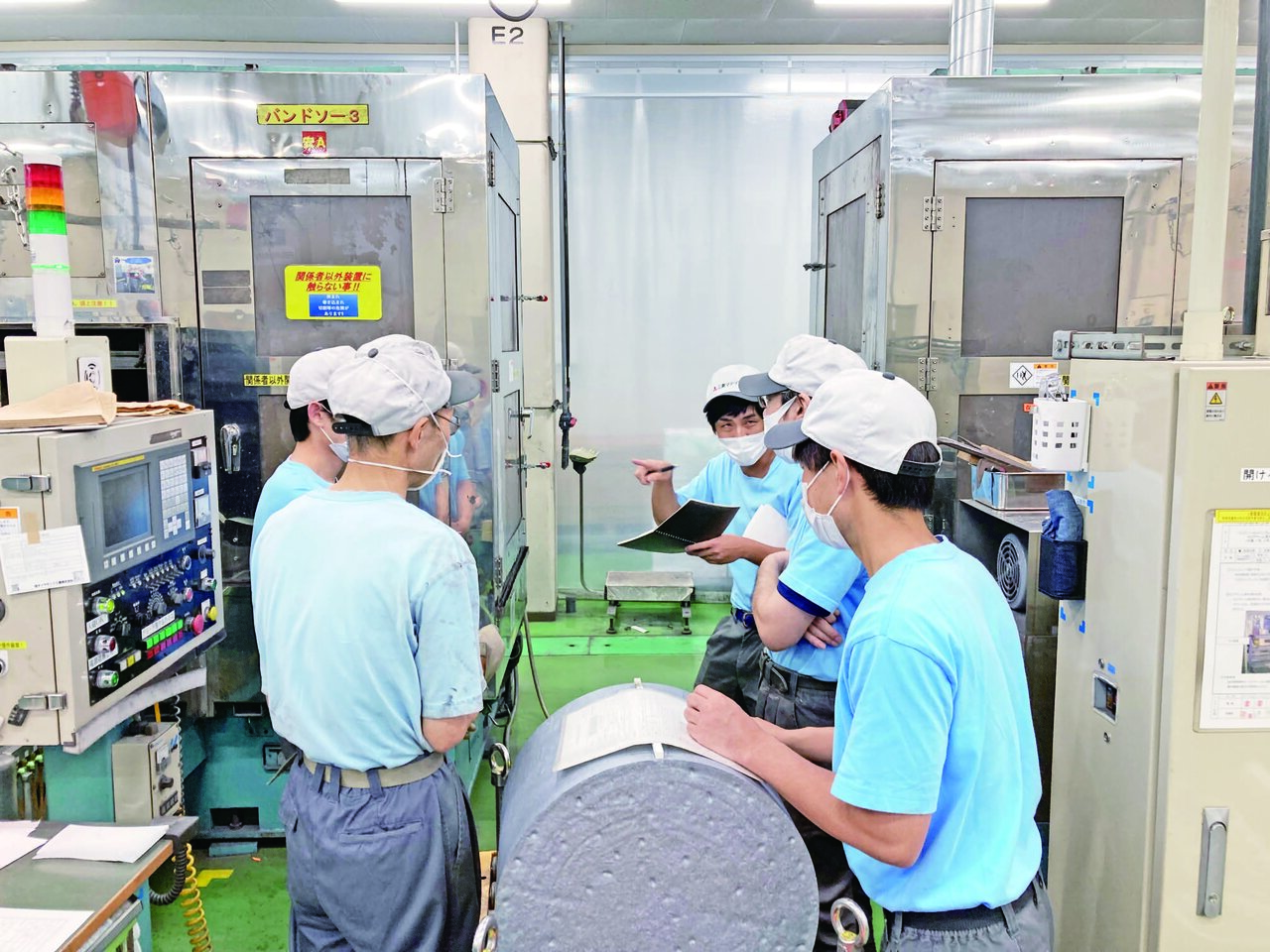
We value the opinions of all team members.
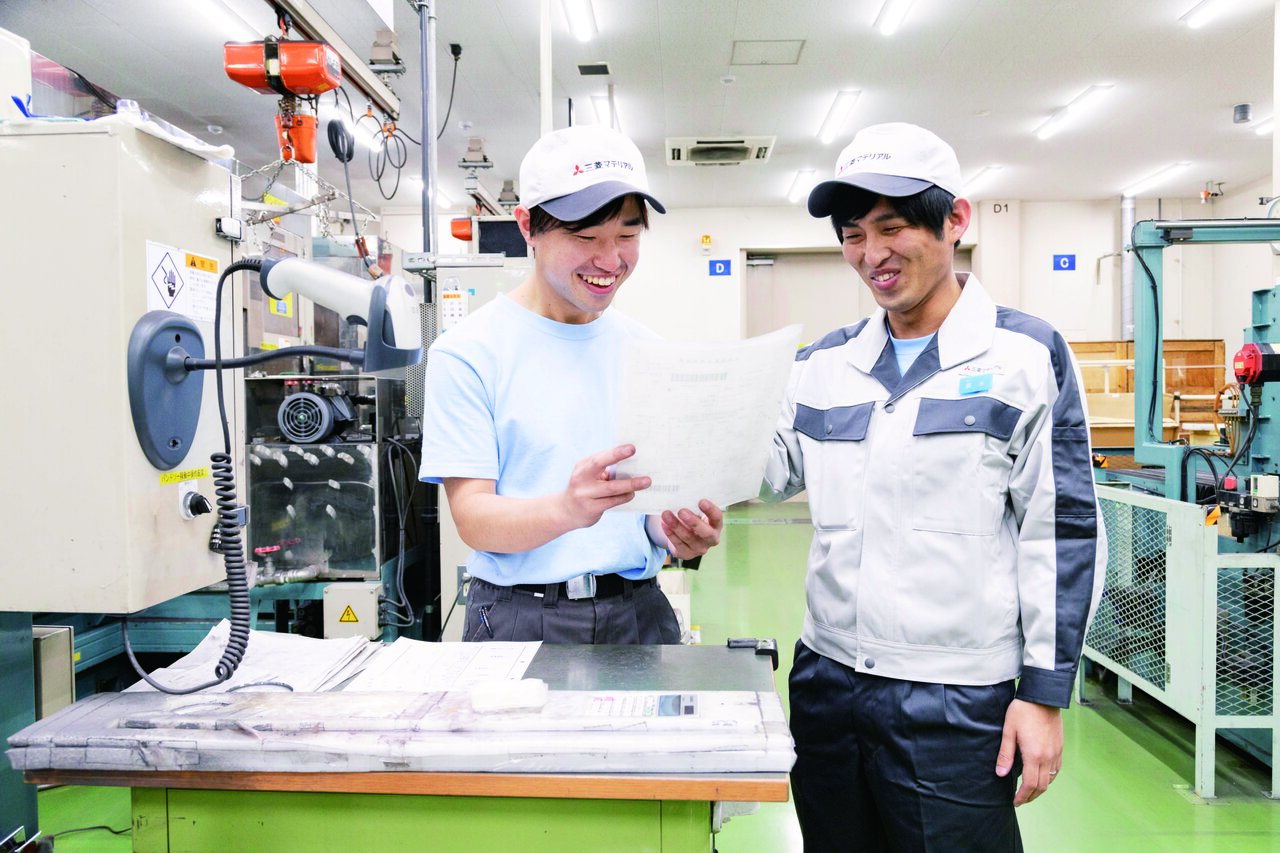
As a team, we try to communicate openly every day so everyone’s opinions can be properly heard.