Special feature : Becoming the Strength of the World's Manufacturing vol.2
Project Story 1 Leveraging our technology and experience to realize the FY2031 Strategy
Solving Difficulties in Machining through the Power of Technology
In the FY2031 Strategy, Mitsubishi Materials aims to leverage its longstanding technology and experience to focus on the development of products in the areas of “difficult-to-cut materials” and “difficult machining.” One of these challenges was the successful development of DVAS, a TRISTAR drill series that uses advanced technology to drill tiny, deep holes in difficult-to-cut materials.
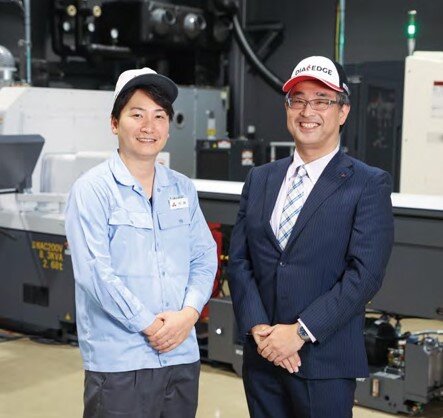
(Left) Akira Sato
Assistant to the Manager, Tool Development Section Drill, CBN & PCD Products Development Dept.
Gifu Plant
Metalworking Solutions Company
(Right) Koji Enami
Small Parts Machining Expert,
Assistant General Manager, Technical Sales Dept. Sales Div.
Metalworking Solutions Company
The development of DVAS, a TRISTAR drill that challenges conventions in small-hole making
Creating next- generation tools that solve machining issues with our precise technology and challenging spirit
Machining refers to using tools to cut or drill holes in metal and other materials. Among these processes, drilling holes is very common. In particular, it plays a key role in creating holes for screws and bolts in the production of precision components used in industries like automotive and medical devices. In addition, these precision components often require special metal materials that are solid or difficult to machine.
These materials require careful machining, leading to a need for higher-performance tools.
To enable careful drilling of holes, Mr. Sato and Mr. Enami took on the challenge of developing a next-generation tool called DVAS. DVAS is a long, slim drill used not only for machining parts in automobiles and medical devices but also for drilling holes in everyday fixtures like water heaters and bath- room fittings like bidet seats. In general, when drilling holes in metals, cutting fluid is used to prevent tool wear and damage due to frictional heat and to keep the tool cool. DVAS incorporates tiny triangle-shaped holes that spiral through the drill, allowing the cutting fluid to flow through. Consequently, in the design and manufacturing process, the team faced a new challenge that had not existed before—to improve tool rigidity without breaking these holes. Mitsubishi Materials achieved a unique design that ensures the tiny spiral holes remain intact, successfully balancing the enhancement of tool rigidity with the ease of removing scrap chips. This development resulted in the creation of a tool that improves our customers’ manufacturing efficiency.
These materials require careful machining, leading to a need for higher-performance tools.
To enable careful drilling of holes, Mr. Sato and Mr. Enami took on the challenge of developing a next-generation tool called DVAS. DVAS is a long, slim drill used not only for machining parts in automobiles and medical devices but also for drilling holes in everyday fixtures like water heaters and bath- room fittings like bidet seats. In general, when drilling holes in metals, cutting fluid is used to prevent tool wear and damage due to frictional heat and to keep the tool cool. DVAS incorporates tiny triangle-shaped holes that spiral through the drill, allowing the cutting fluid to flow through. Consequently, in the design and manufacturing process, the team faced a new challenge that had not existed before—to improve tool rigidity without breaking these holes. Mitsubishi Materials achieved a unique design that ensures the tiny spiral holes remain intact, successfully balancing the enhancement of tool rigidity with the ease of removing scrap chips. This development resulted in the creation of a tool that improves our customers’ manufacturing efficiency.
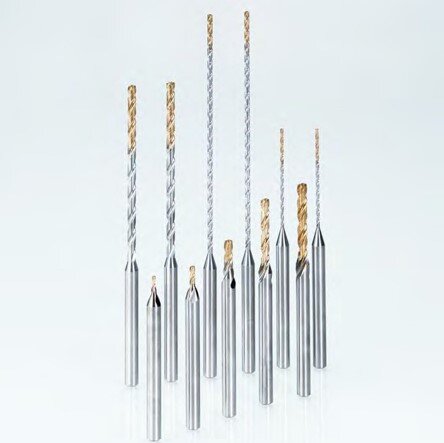
“Conventional cutting tools tend to have reduced uptime due to break- age and damage,” explains Mr. Sato, who was involved in the development. “Preventing breakage contributes to enhancing productivity and stabilizing quality. We tried to create a tool that can support not only conventional machining techniques but also new ones such as LFV (Low Frequency Vibration Cutting) technology to contribute to our customers’ manufacturing.”
DVAS is compatible with machines equipped with LFV technology. LFV technology is the latest advancement designed to address issues related to scrap chip troubles that arise during metalworking. Scrap chips have long been an obstacle in metalworking due to getting caught in tools and damaging machined materials. However, DVAS combined with LFV technology solves these problems.
Behind the success of this chal- lenging development was the on-site expertise and continuous trial and error of the professionals who carried out advanced technical development and produced a drill that incorporates unique, industry-first technology.
“Our mission is to identify our cus- tomers’ on-site problems and provide solutions,” says Mr. Enami, who is in charge of technical sales. “To achieve this, we initiated collaborative seminars with machine tool builders and peripheral equipment manufacturers to make the capabilities of our products, including TRISTAR drills, more widely known among customers. With unparalleled product capabilities and solution offerings that other companies cannot replicate, we will work toward the realization of the FY2031 Strategy.”
Mr. Sato adds: “We aim to be a man- ufacturer capable of swiftly delivering the tools our customers expect. We will expand our tool lineup to meet various demands, including small-hole, large- hole, and deep-hole drilling, and offer them to the market without any delays. Additionally, through our proprietary technical support, we intend to expand the tools market and contribute to the realization of the FY2031 Strategy.”
DVAS is compatible with machines equipped with LFV technology. LFV technology is the latest advancement designed to address issues related to scrap chip troubles that arise during metalworking. Scrap chips have long been an obstacle in metalworking due to getting caught in tools and damaging machined materials. However, DVAS combined with LFV technology solves these problems.
Behind the success of this chal- lenging development was the on-site expertise and continuous trial and error of the professionals who carried out advanced technical development and produced a drill that incorporates unique, industry-first technology.
“Our mission is to identify our cus- tomers’ on-site problems and provide solutions,” says Mr. Enami, who is in charge of technical sales. “To achieve this, we initiated collaborative seminars with machine tool builders and peripheral equipment manufacturers to make the capabilities of our products, including TRISTAR drills, more widely known among customers. With unparalleled product capabilities and solution offerings that other companies cannot replicate, we will work toward the realization of the FY2031 Strategy.”
Mr. Sato adds: “We aim to be a man- ufacturer capable of swiftly delivering the tools our customers expect. We will expand our tool lineup to meet various demands, including small-hole, large- hole, and deep-hole drilling, and offer them to the market without any delays. Additionally, through our proprietary technical support, we intend to expand the tools market and contribute to the realization of the FY2031 Strategy.”
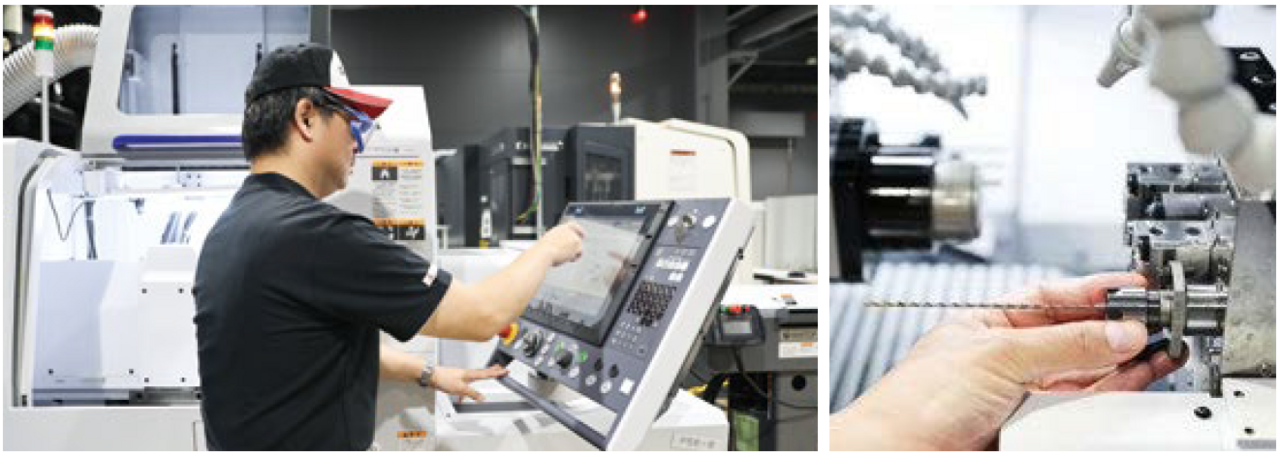
(Left) Mr. Enami checking a machining tool capable of supporting the LFV technology
(Right) DVAS attached to a machine tool allows for the drilling of tiny, deep holes.
What are “difficult-to-cut materials” and “difficult machining”?
Difficult-to-cut materials refers to materials that are inherently challenging to machine. Examples include stainless steel, titanium alloys, and heat-resistant alloys. These materials play an important role in the automotive and aircraft industries, where strength and heat resistance are crucial. Difficult machining, on the other hand, refers to fields where machining becomes challenging due to the shape of the workpiece or the complexity introduced by new machining processes. It includes processes such as machining small holes, deep holes, dense, complex, microscopic shapes, and precision machining that requires high accuracy.
What is LFV technology?
LFV technology is a proprietary control technology developed by Citizen Machinery Co., Ltd. It involves vibrating the tool in the cutting direction and synchronizing this vibration with the rotation of the spindle while cutting. Its distinctive feature lies in the ability to forcibly separate the material being cut and the cutting tool with fine vibrations, resulting in the fragmentation and discharge of previously connected scrap chips. This prevents issues caused by scrap chips and a rise in the temperature of the tool’s cutting edge.
LFV is a registered trademark of Citizen Watch Co., Ltd.
LFV is a registered trademark of Citizen Watch Co., Ltd.