Special feature : Becoming the Strength of the World's Manufacturing vol.3
Project Story 2 Leveraging our technology and experience to realize the FY2031 Strategy
Innovating Manufacturing Sites with Digital Technology
In Mitsubishi Materials’ FY2031 Strategy, the Metalworking Solutions business has set the target of becoming “a leading company in tungsten products recognized by customers globally.” To achieve this and address diverse needs across manufacturing sites, we aim to develop cutting tools with innovative functions and provide an extensive range of machining solution services leveraging the digital technology accumulated at our technical centers worldwide. As examples of these initiatives, we will introduce the development of sensor tools and the global expansion of our technical centers.
What is a sensor tool?
A sensor tool is a type of cutting tool equipped with two types of sensors: a displacement sensor, which measures the dimensions of the material being cut, and an image sensor, which photographs the machined surface. These sensors allow for immediate measurement and automatic adjustment of workpiece dimensions, as well as capturing images of the machined surface, immediately after machining. Furthermore, analyzing the surface images allows for automatic assessment of tool life.
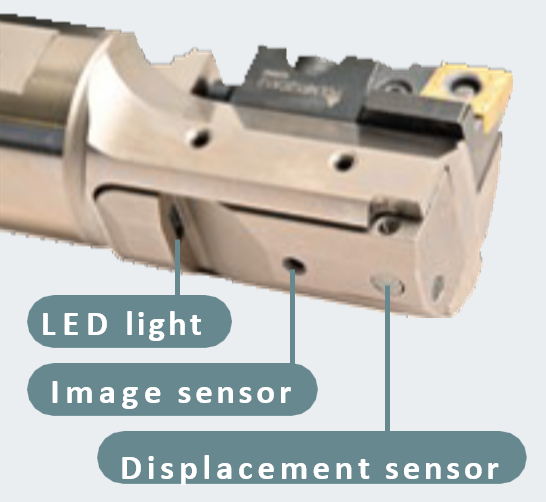
Development of sensor tools
Quality, cost, and productivity. Aiming to create a tool that can solve various problems our customers face.
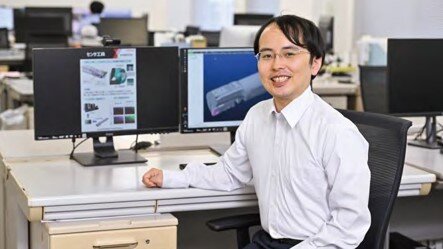
Wataru Takahashi
Technology Development & Tools Data Section Machining Technology Center
Research & Development Div. Metalworking Solutions Company
As a leading company of the carbide tools industry, Mitsubishi Materials is working on digitalizing machining. The sensor tools we are developing play an integral role in this digitalization process.
Our sensor tools feature two types of sensors, a displacement sensor and an image sensor. The conventional process of measuring workpieces involves replacing the cutting tool on the machining equipment with a dedicated measurement sensor, or removing the workpiece to set it on a separate measuring device. However, with a displacement sensor, measurements can be conducted on the machine immeditely after machining, leading to improved productivity. Additionally, unlike conventional tools that are typically replaced once a certain production volume is reached, sensor tools can be utilized until the limits of their tool life, enabling cost reduction. Furthermore, we can assess and quantify the deterioration in the quality of the machined surface previously evaluated through human eyesdirectly on the machining equipment. This allows us to pass on engineers’ know-how more easily.
During the development process of these sensor tools, we faced numerous challenges. For example, the image sensor needed to be compact but support high resolutions and fit into a small space. Similarly, the displacement sensor needed to be compact and highly precise. Therefore, we collaborated with the Innovation Center, which has abundant knowledge in this field, to select components and develop electronic circuits, leading to our current specifications. In the future, we will develop sensor tools with various specifications to meet diverse customer needs. In line with this goal, we hope that our customers at manufacturing sites adopt our sensor tools at the earliest opportunity to address their on-site issues through our machining solutions.
Our sensor tools feature two types of sensors, a displacement sensor and an image sensor. The conventional process of measuring workpieces involves replacing the cutting tool on the machining equipment with a dedicated measurement sensor, or removing the workpiece to set it on a separate measuring device. However, with a displacement sensor, measurements can be conducted on the machine immeditely after machining, leading to improved productivity. Additionally, unlike conventional tools that are typically replaced once a certain production volume is reached, sensor tools can be utilized until the limits of their tool life, enabling cost reduction. Furthermore, we can assess and quantify the deterioration in the quality of the machined surface previously evaluated through human eyesdirectly on the machining equipment. This allows us to pass on engineers’ know-how more easily.
During the development process of these sensor tools, we faced numerous challenges. For example, the image sensor needed to be compact but support high resolutions and fit into a small space. Similarly, the displacement sensor needed to be compact and highly precise. Therefore, we collaborated with the Innovation Center, which has abundant knowledge in this field, to select components and develop electronic circuits, leading to our current specifications. In the future, we will develop sensor tools with various specifications to meet diverse customer needs. In line with this goal, we hope that our customers at manufacturing sites adopt our sensor tools at the earliest opportunity to address their on-site issues through our machining solutions.
Global expansion of technical centers
Continuously improving issues faced by manufacturing sites through the provision of customized solutions
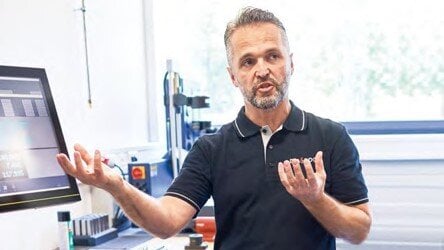
MTEC Stuttgart Assistant Manager
Shpend Arifi
In recent years, the metalworking industry has faced various challenges, including labor shortages, and custom- ers are expecting suppliers to provide value-added services. Among these requirements, reducing costs and increasing productivity is not just about improving the production process, but also necessitates a review of the plan- ning phase.
This is why Mitsubishi Materials has established technical centers around the world to provide support to customers. The overseas technical centers focus on providing customized soluions for local customers. Established in 2019, the MTEC Stuttgart in Germany aims to provide solution services to address issues for customers across Europe. By introducing a European standard of tools and solutions, MTEC Stuttgart offers customers an even broader product portfolio to better meet their needs.
One of our objectives is to continu- ously improve our customers’ issues. To this end, we must continue to offer added value to our customers through optimized technical support, utilizing next generation cutting tools and digital analysis, as well as technical training and process optimization.
In order to continuously offer advanced services, we are combining MTEC Stuttgart’s expertise with the technological know-how of our colleagues in Japan, and also exploring the potential of open innovation by strategically collaborating with external experts and research institutions. By leveraging Mitsubishi Materials’ latest digital tools, we will aim to rapidly de- liver solutions that are better tailored to each customer than ever before.
This is why Mitsubishi Materials has established technical centers around the world to provide support to customers. The overseas technical centers focus on providing customized soluions for local customers. Established in 2019, the MTEC Stuttgart in Germany aims to provide solution services to address issues for customers across Europe. By introducing a European standard of tools and solutions, MTEC Stuttgart offers customers an even broader product portfolio to better meet their needs.
One of our objectives is to continu- ously improve our customers’ issues. To this end, we must continue to offer added value to our customers through optimized technical support, utilizing next generation cutting tools and digital analysis, as well as technical training and process optimization.
In order to continuously offer advanced services, we are combining MTEC Stuttgart’s expertise with the technological know-how of our colleagues in Japan, and also exploring the potential of open innovation by strategically collaborating with external experts and research institutions. By leveraging Mitsubishi Materials’ latest digital tools, we will aim to rapidly de- liver solutions that are better tailored to each customer than ever before.
Technical centers supporting customers worldwide
We have technical centers around the world to provide technical support to our customers. We established MTEC Stuttgart in Stuttgart, Germany in June 2019, and MTEC Pune, our ninth technical center, in India in March 2020. Through the close collaboration of technical centers worldwide, we will swiftly deliver customer- oriented solutions.
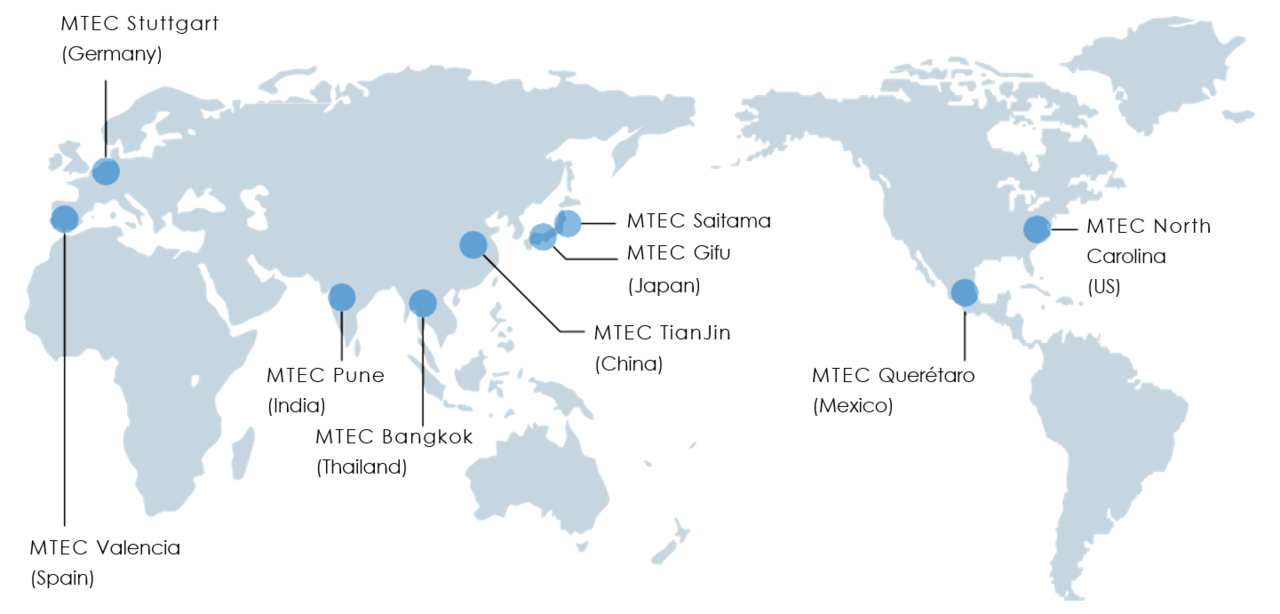