Special feature : Becoming the Strength of the World's Manufacturing vol.4
Project Story 3 Circulating resources to realize the FY2031 Strategy
Making Tungsten Procurement Sustainable
Tungsten is a primary raw material for carbide tools. It has also seen increased demand in recent years, particularly as a material for rechargeable batteries used in products such as electric vehicles (EVs). With the aim of sustainable tungsten procurement, Mitsubishi Materials Group is striving to expand the collection of tungsten carbide scrap globally and strengthen its recycling processing capacity.
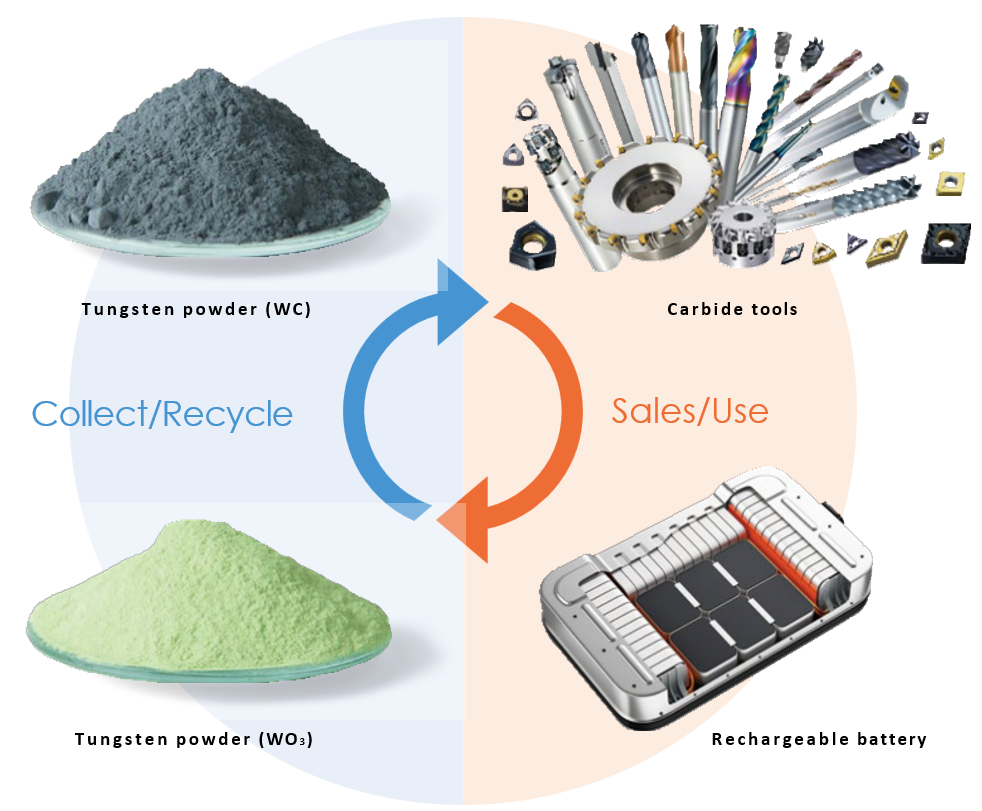
What is tungsten?
Tungsten is an extremely hard and heavy rare metal. When combined with carbon, it forms an even harder material. It is this hardness that makes it an ideal primary raw material for carbide tools. Additionally, tungsten powder is also used as a material for rechargeable batteries, and with the increasing electrification of vehicles, the demand for tungsten is expected to rapidly expand in the future.
Aiming for a recycled raw material ratio of 80% or more
Mitsubishi Materials Group is strengthening its recycling processing capacity for collected carbide tools. At the Akita Plant of our Group company, Japan New Metals, tungsten recycling facilities were expanded in 2017, resulting in a substantial increase in processing capacity. Our aim is to increase the ratio of recycled raw materials used in the production of carbide tools to over 80% by FY2031. To this end, we are actively engaged in the development of recycling technology and the expansion of recycling capacity.
Collecting used carbide tools from around the world and utilizing them without waste
Tungsten is concentrated in specific resource-rich countries, with China being the main source. Due to its high rarity and the risk of unavailability due to changes in global conditions, it is imperative to work on establishing a recycling system to ensure a stable supply of this raw material.Mitsubishi Materials is establishing a resource recycling system to collect used carbide tools and other carbide scrap from around the world and transform them into new tungsten powder. We are currently expanding our collection efforts in North and South America, with plans to further extend scrap collec- tion in Europe in the future.
Establishment of a resource recycling system
Aiming to provide a stable supply of tungsten powder to meet the growing demand in society
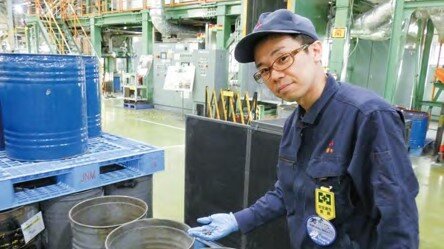
Yuta Umeta
Deputy Manager of Manufacturing Group Akita Plant
Japan New Metals Co., Ltd.
At our Akita Plant, we recycle tungsten concentrates and tungsten-containing scrap to produce tungsten powder through an integrated production process. Currently, I am leveraging my experience in technical development to manage the integrated production line.
Towards the achievement of the FY2031 Strategy, our company is dedicated to strengthening recycling capabilities. The completion of our new tungsten recycling plant in 2017 allowed us to double our recycling capacity for carbide scraps. Currently, the annual recycling capacity for carbide scrap stands at approximately 1,000 tons. To expand recycling efforts, it is necessary to increase the procurement of carbide scrap. We are currently working with domestic and overseas Group companies to establish a scrap collection system. In order to ensure stable procurement routes, we are coordinat- ing with multiple procurement sources.
Furthermore, our company provides tungsten powder not only for tungsten carbide alloys but also for various other applications. In particular, we can feel the future potential of tungsten through the demand for electronic components and rechargeable batteries. Growth in these sectors will contribute to the achievement of the FY2031 Strategy. To that end, I feel that it is important to keep up with the latest cutting-edge technologies in society through information and technical exchanges with customers in new fields.
We will continue to improve our refining technologies to meet the growing demand in society, striving for improved quality and cost reduction of high-purity and high-value-added products. As a trusted powder raw material manufacturer, we are committed to providing a stable supply of tungsten powder to customers in the processing fields that support manufacturing.
Towards the achievement of the FY2031 Strategy, our company is dedicated to strengthening recycling capabilities. The completion of our new tungsten recycling plant in 2017 allowed us to double our recycling capacity for carbide scraps. Currently, the annual recycling capacity for carbide scrap stands at approximately 1,000 tons. To expand recycling efforts, it is necessary to increase the procurement of carbide scrap. We are currently working with domestic and overseas Group companies to establish a scrap collection system. In order to ensure stable procurement routes, we are coordinat- ing with multiple procurement sources.
Furthermore, our company provides tungsten powder not only for tungsten carbide alloys but also for various other applications. In particular, we can feel the future potential of tungsten through the demand for electronic components and rechargeable batteries. Growth in these sectors will contribute to the achievement of the FY2031 Strategy. To that end, I feel that it is important to keep up with the latest cutting-edge technologies in society through information and technical exchanges with customers in new fields.
We will continue to improve our refining technologies to meet the growing demand in society, striving for improved quality and cost reduction of high-purity and high-value-added products. As a trusted powder raw material manufacturer, we are committed to providing a stable supply of tungsten powder to customers in the processing fields that support manufacturing.