Special feature : Evolving copper Vol.3
Advancing Talent and Manufacturing Sites
Aiming to become the Global First Supplier
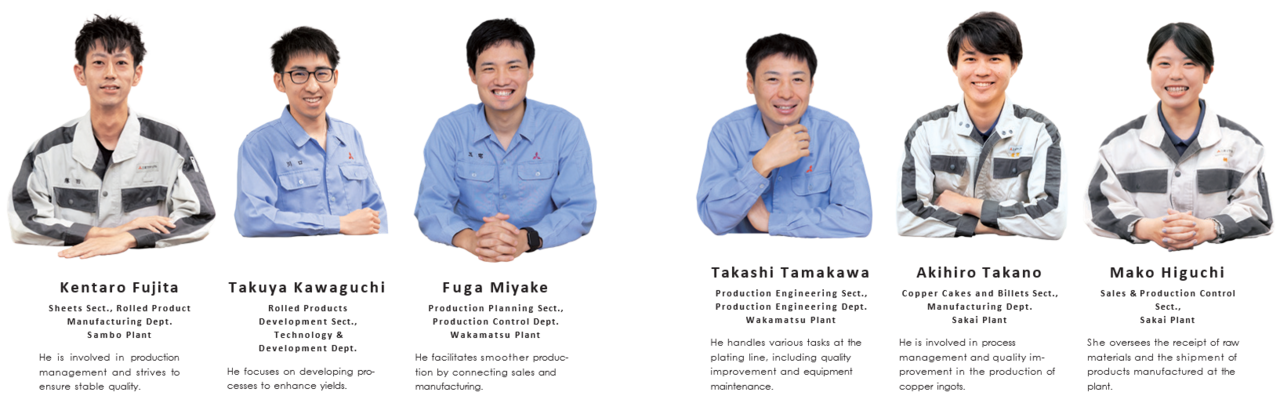
Each site worked together to establish a higher capacity production system

Takano
At the Copper Cakes and Billets Sect. of the Sakai Plant, we plan to increase the copper ingot production volume by 30% compared to previous levels. To achieve this, we are working on operating and leveraging new melting facilities and speeding up casting to increase the production volume per unit time. Since speeding up casting requires enhancing facility capacity and improving equipment and compo- nents, we incorporate actual workers’ insights to prevent defects.
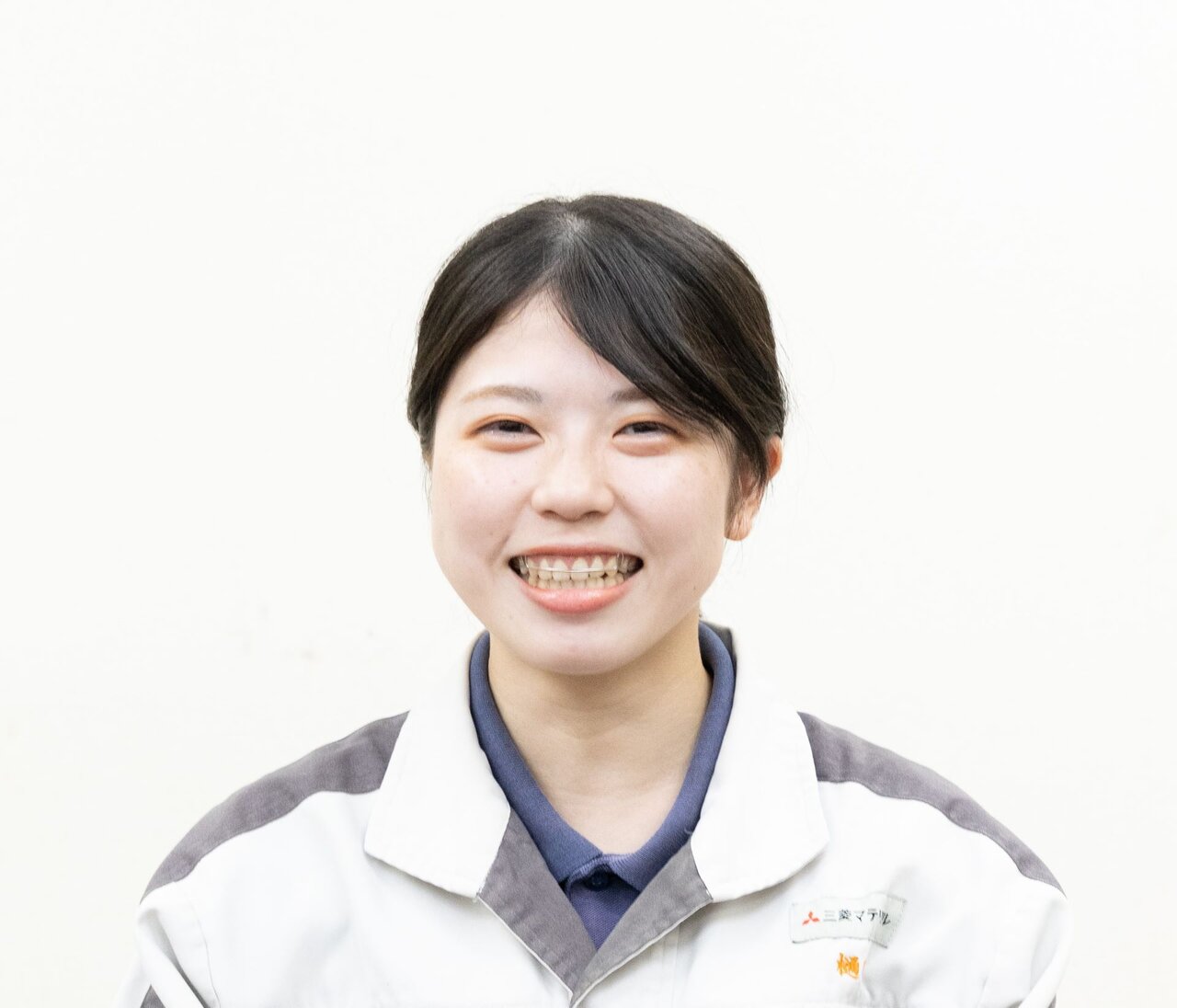
Higuchi
At the Sales & Production Control Sect. of the Sakai Plant, we aim to raise the copper recycling rate so that alloy scraps generated through machining are circulated internally. We send these alloy scraps to Naoshima Smelter & Refinery and Onahama Smelter & Refinery to ensure that they are reused. This kind of resource circulation has gained attention from customers in recent years. How about the Sambo Plant?
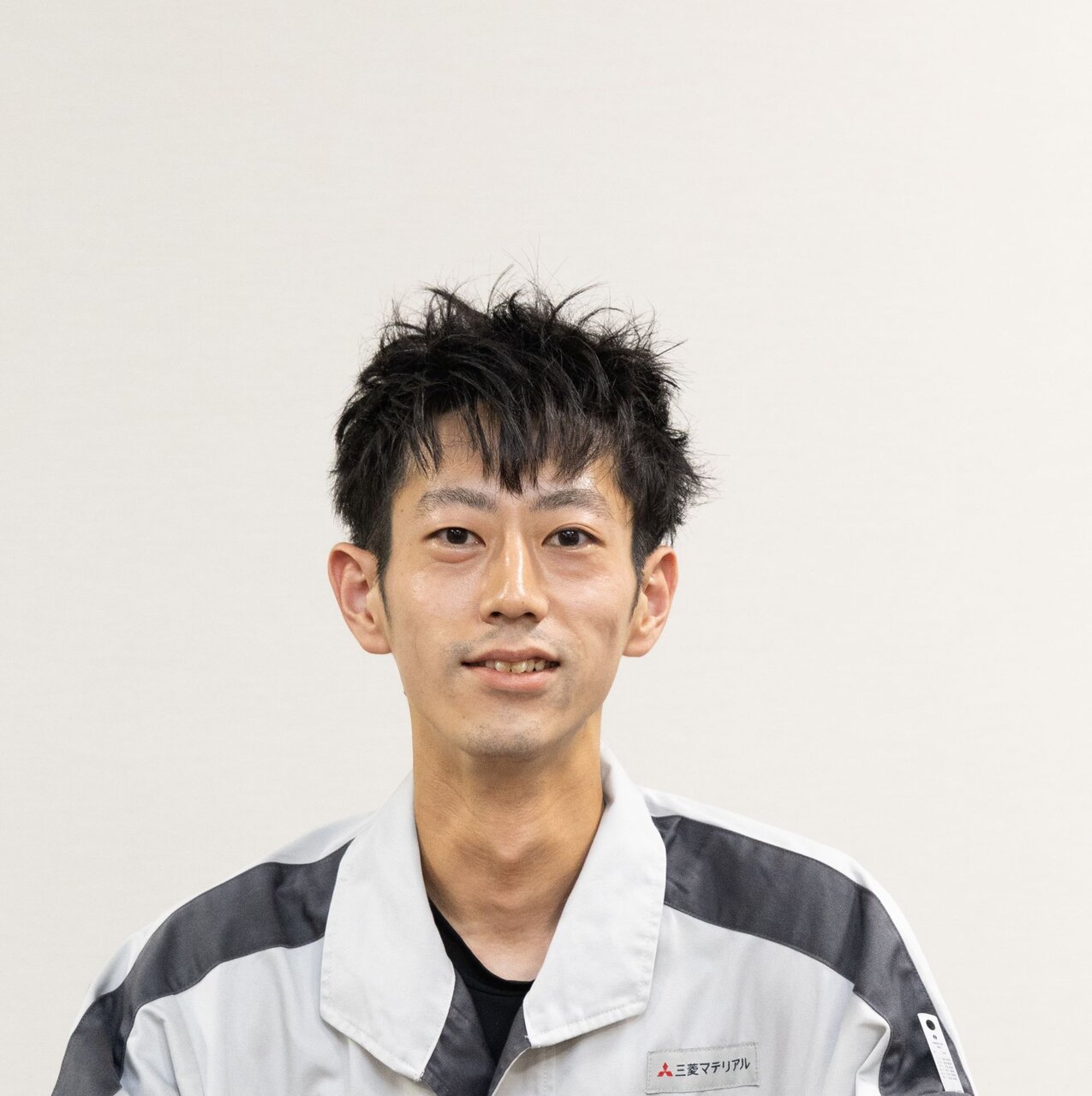
Fujita
At the Sambo Plant, we have prepared the mass production system for rolled products and are cohesively working to achieve targets, including improving yields. I am involved in production management for copper plate products at the Sheets Sect. Currently, I am focused on process management to meet customer deadlines while ensuring stable quality.
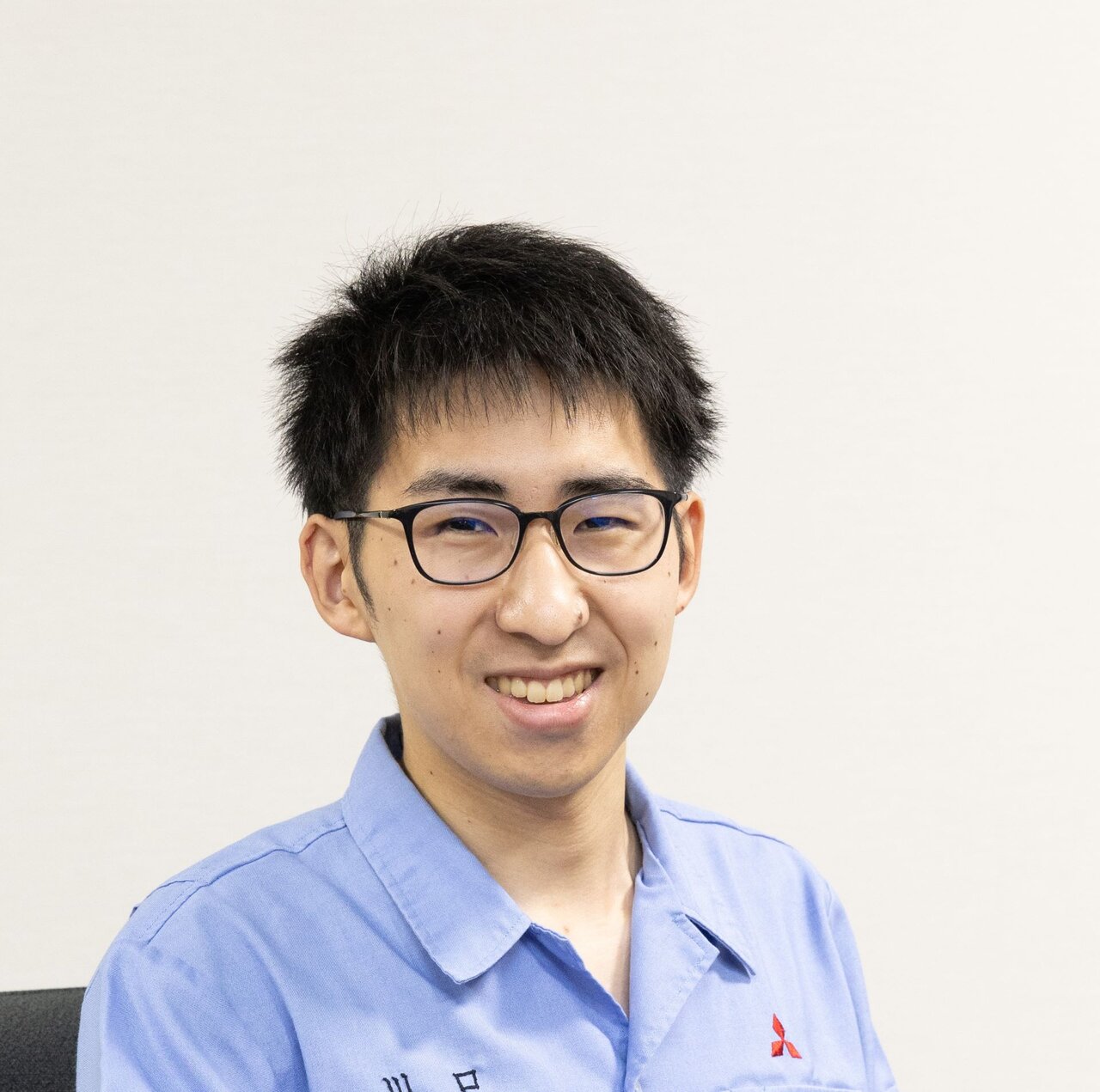
Kawaguchi
At the Technology & Development Dept., we are improving manufacturing processes and expanding sales for developed alloys, such as MOFC®-HR. We are focusing on sales activities for automotive component and electronic equipment manufacturers. Our main focus is on preventing plate warping, which is an issue in improving copper plate yields. How about the Wakamatsu Plant?
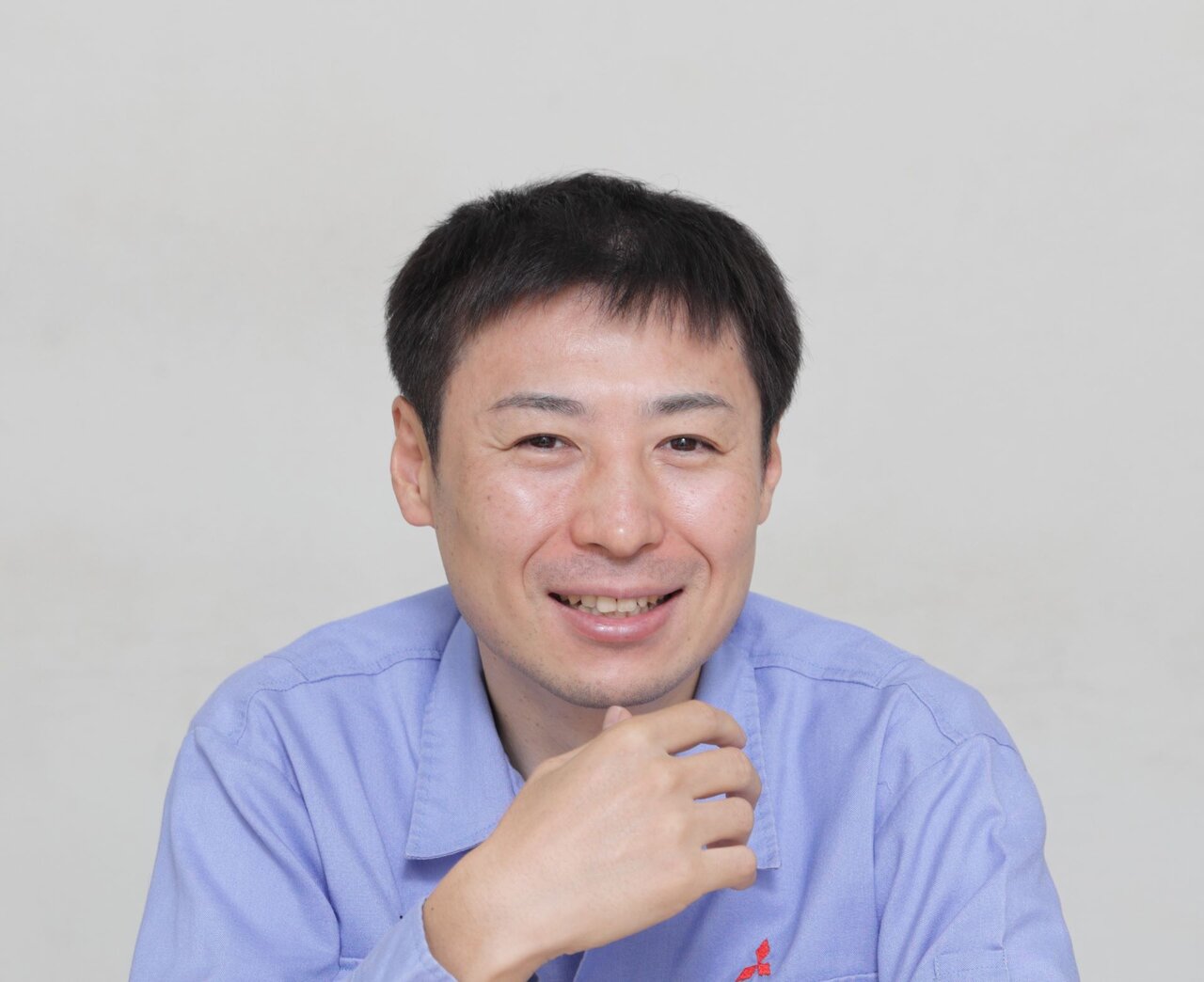
Tamakawa
At the Wakamatsu Plant, we are putting effort into speeding up facilities and reducing defects. I am involved in expanding the reflow tin plating line facilities, having launched the renovation plan for the speed-up last year. It was not a smooth process due to troubles that occurred after the renovation, but we have now entered the mass production stage and are steadily completing the mass production system. Going forward, it is essential to expand facilities with a sense of speed.
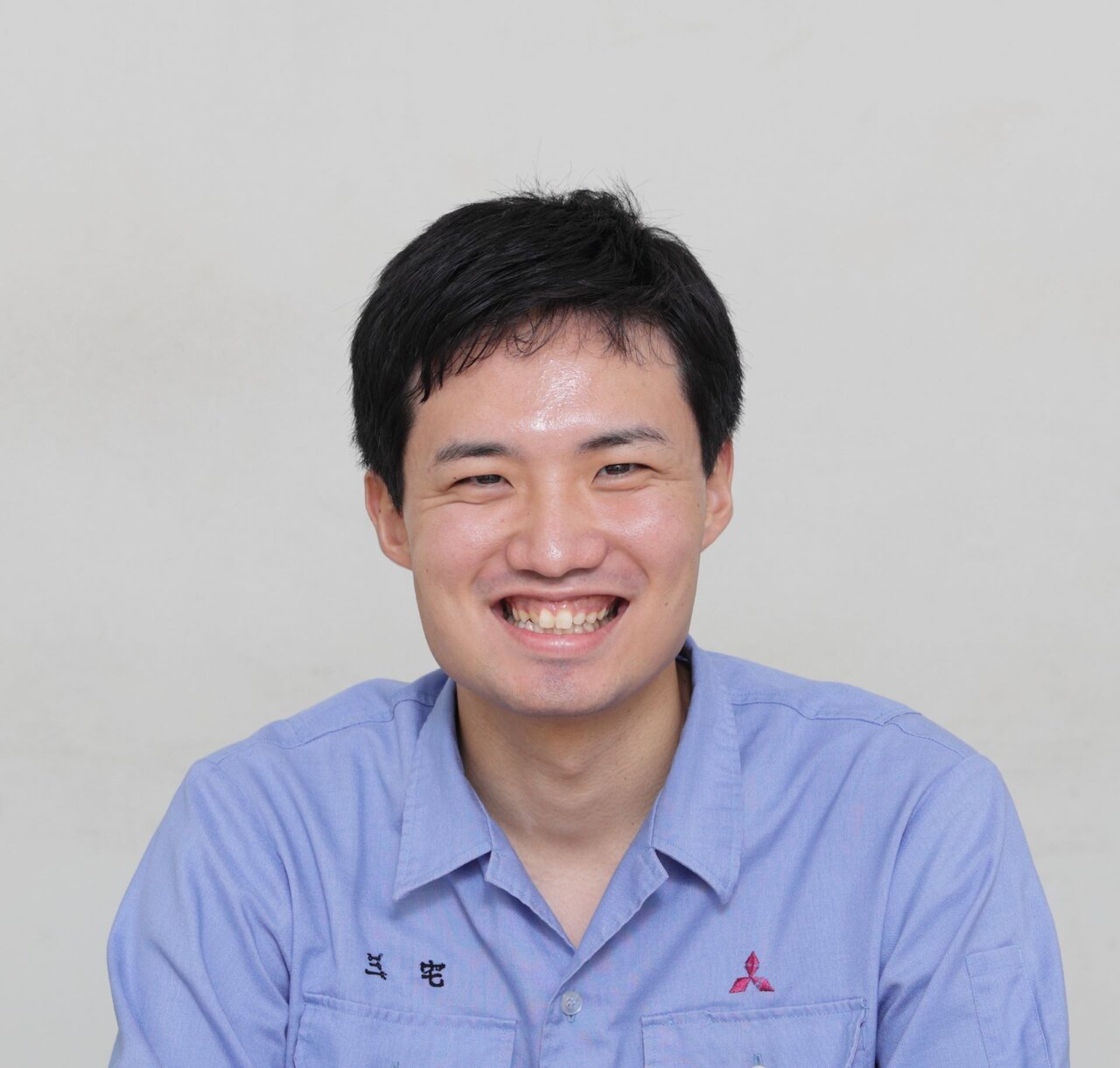
Miyake
As a member of the Production Control Dept., I connect sales and manufacturing, communicating customer orders to the manufacturing sites. I act as a liaison between the two parties to prevent any delays. We are gaining more new customers and meeting the demand for finished copper products, including automotive applications.
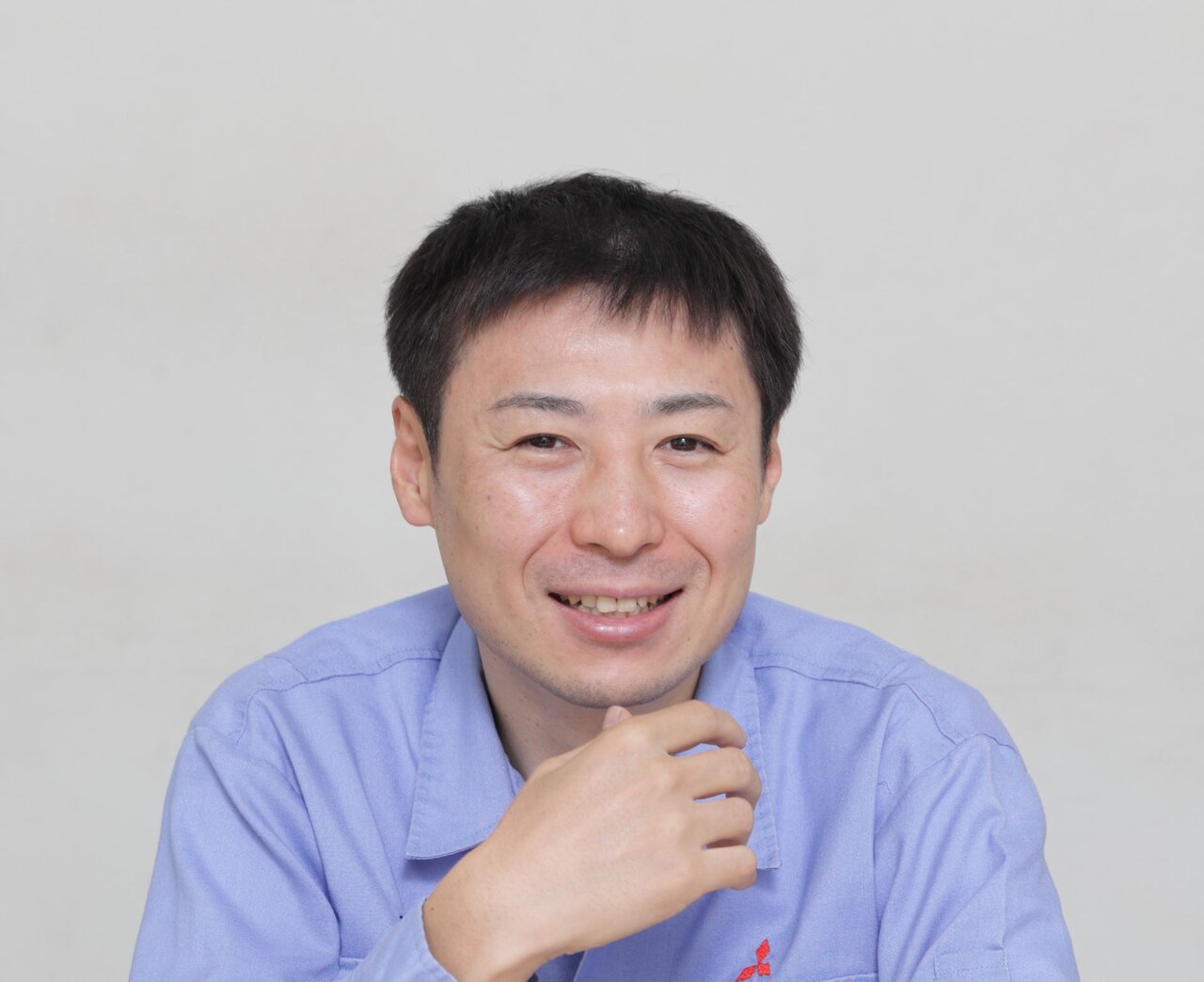
Tamakawa
Speeding up facilities presents some challenges. It reduces the available time for workers and increases their workloads. Therefore, we needed to simultaneously automate operations to lighten their burdens.
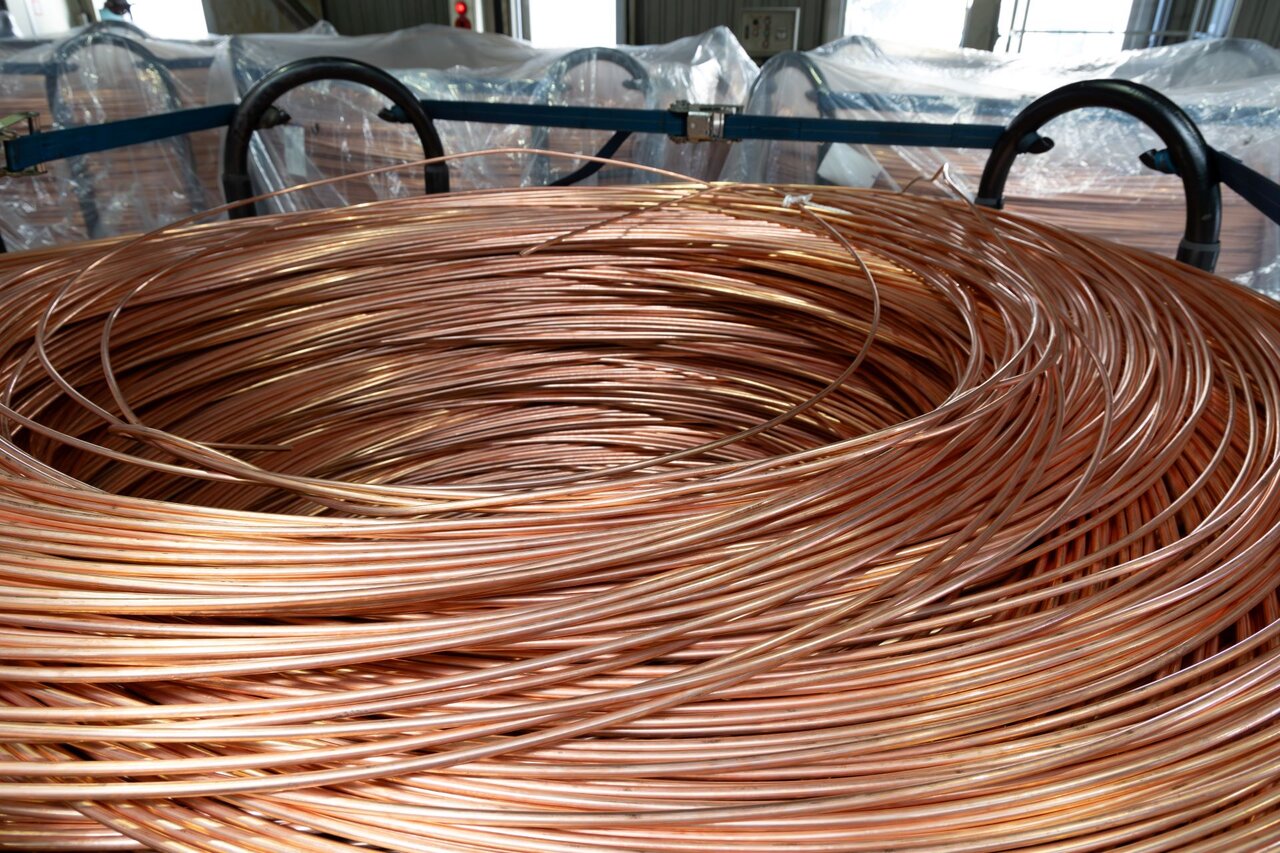

We want to share insights and enhance our collaborative power

Kawaguchi
To enhance processes, we share pain points across departments and exchange opinions to drive improvements. For example, we can simulate process improvements at the Copper & Copper Alloy Development Center or seek help from the Sheets Sect. of the Sambo Plant, where Mr. Fujita works. I believe these are strengths unique to our company. Additionally, the Technology & Development Dept., to which I belong, has three locations in Japan and holds monthly technical interaction meetings to exchange opinions and introduce each other’s work. Moving forward, I would like to see even more active interaction to leverage our strengths.
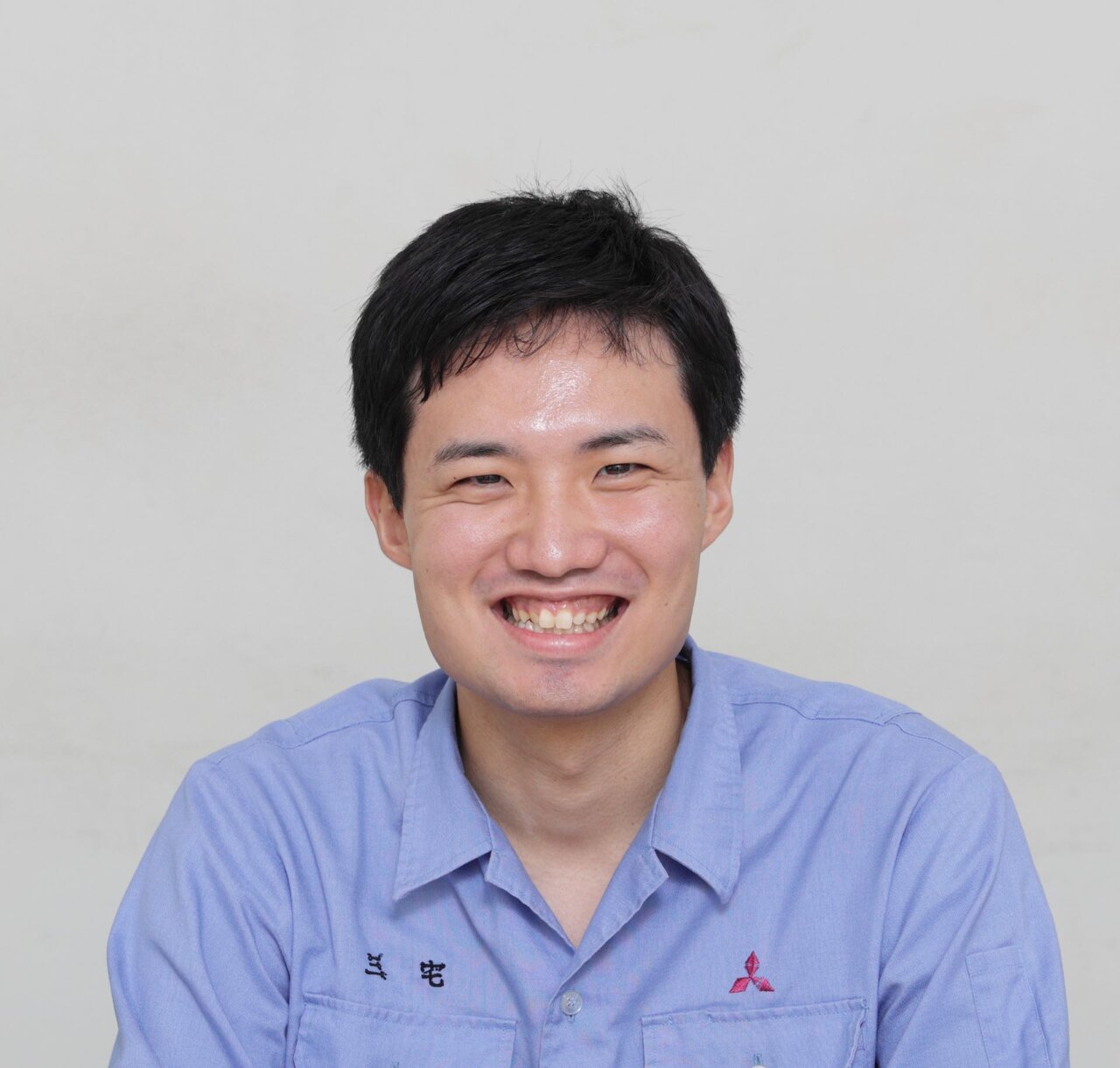
Miyake
Close information sharing with salespeople is key to my job. When I receive information from them, such as forecasts of increased orders for a certain sector, I convey it to manufacturing sites in a timely manner. While predicting orders can be challenging, closer information sharing will enhance our agility.
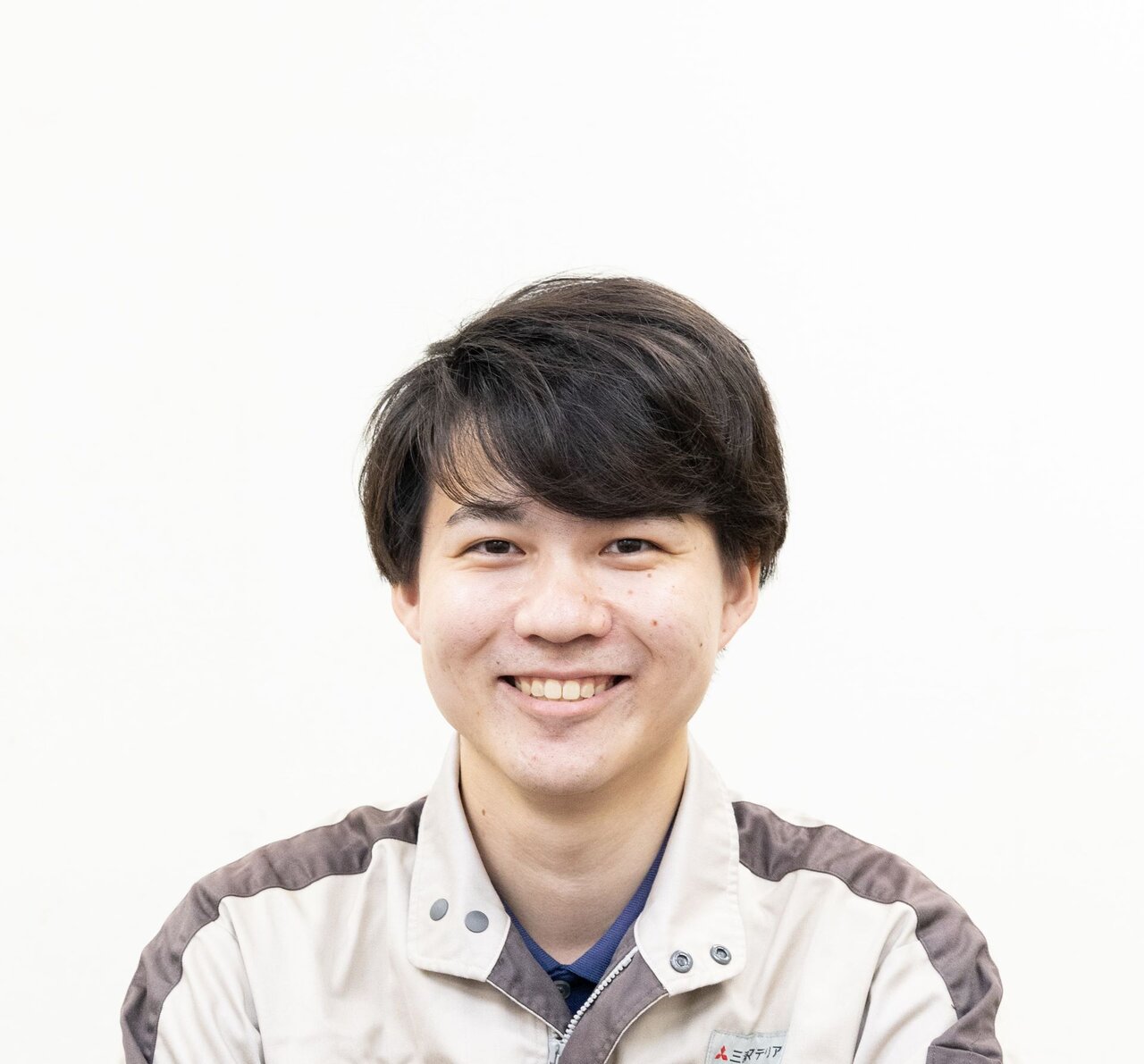
Takano
When we installed a new melting facility at the Sakai Plant, we needed to consider various viewpoints, including legal and budget require- ments, so it was impossible to imple- ment the plan with only engineers. To address this large-scale issue, we formed an interdivisional task force aimed at resolving all relevant con- cerns.
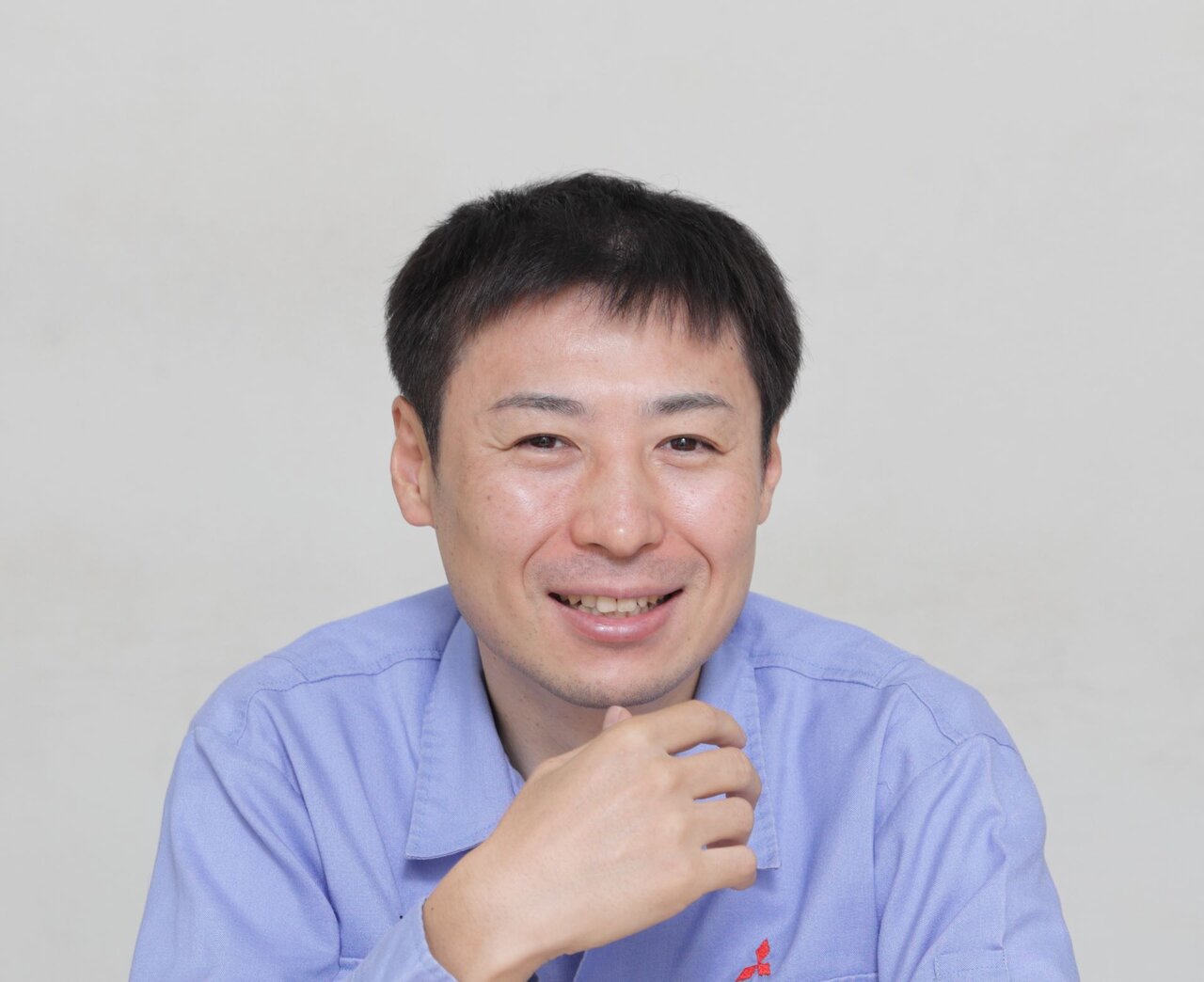
Tamakawa
Since the Sambo, Wakamatsu, and Sakai plants all have similar facilities, the ideal form of collaboration would involve sharing the unique know-how that each site has most like ly developed. By sharing this know-how and incorporating it into operations and process design, we can enhance our company’s collaborative power.

Takano
I find that expectations for our 100% recycled materials are increasing as eco-friendly products. We have recently increased our casting of recycled materials, so we would like to collaborate with the Sambo Plant on this. In addition, the demand for aerospace applications is growing along with social expectations. One of the strengths of our materials is their stable and uniform quality, which fosters trust among customers due to minimal performance fluctuations.
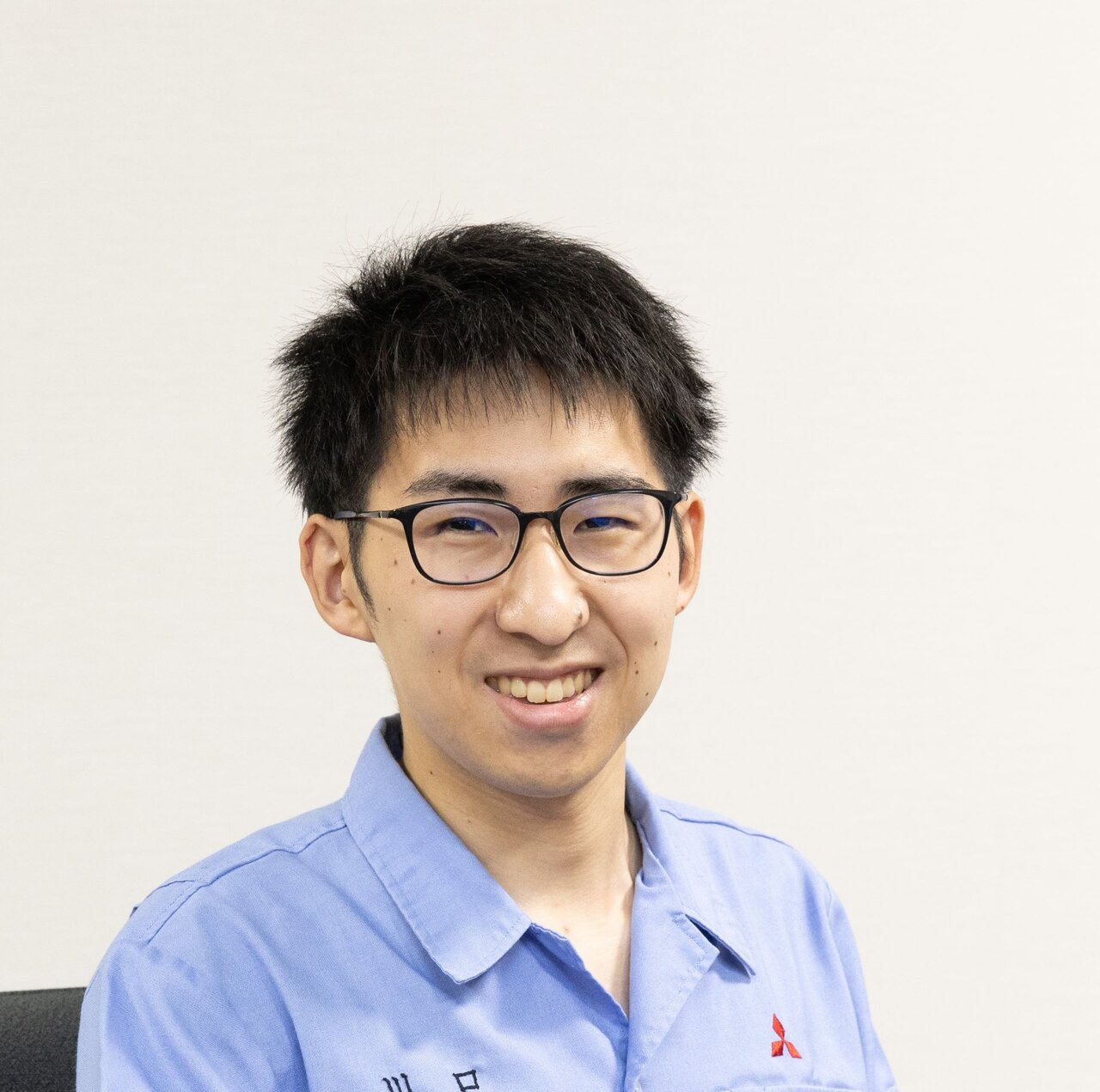
Kawaguchi
Society is looking towards Mitsubishi Materials to strengthen resource circulation. Moving forward, it will be crucial to effectively recycle copper within Japan. To mitigate environmental burdens, our processing sites need to enhance our copper recycling capabilities and establish a solid foundation for resource circulation. I believe this is what society expects from us.
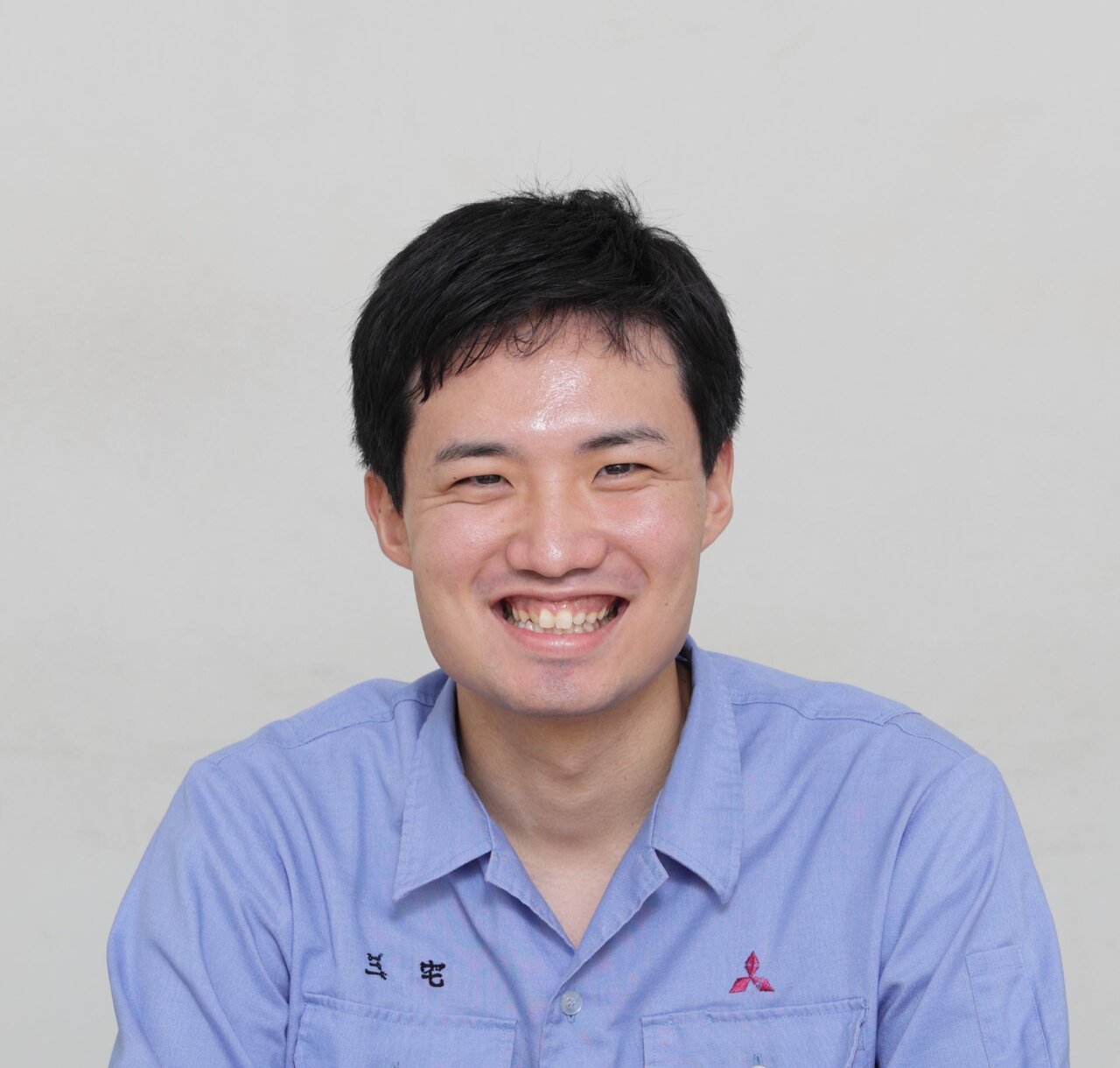
Miyake
Speaking of resource circulation, I previously worked in the Raw Material Section, where I was involved in sending scraps generated at the Wakamatsu Plant to Onahama Smelter & Refinery for casting. By-products generated in-house are reused within the company. This approach will expand the options for raw materials we can utilize. I hope to see more initiatives like this in the future.
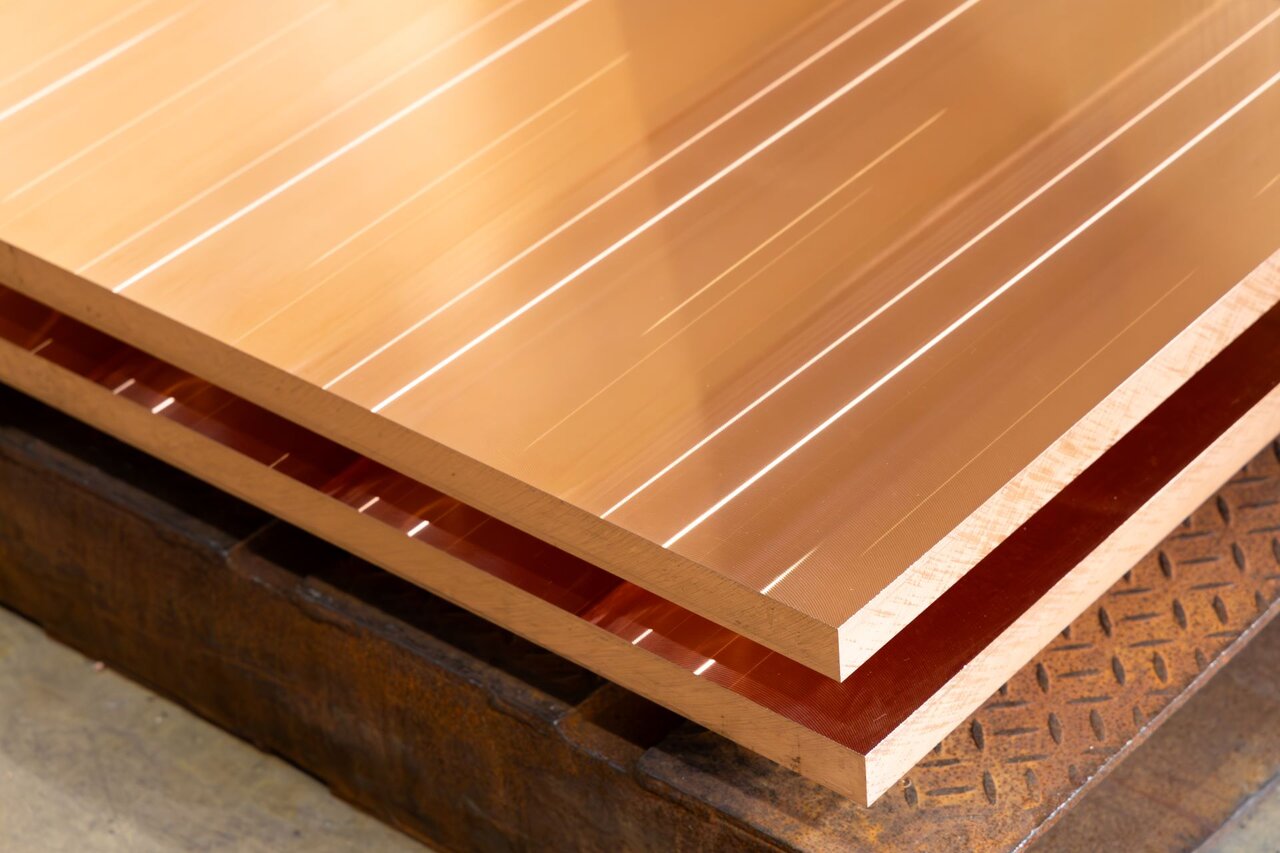
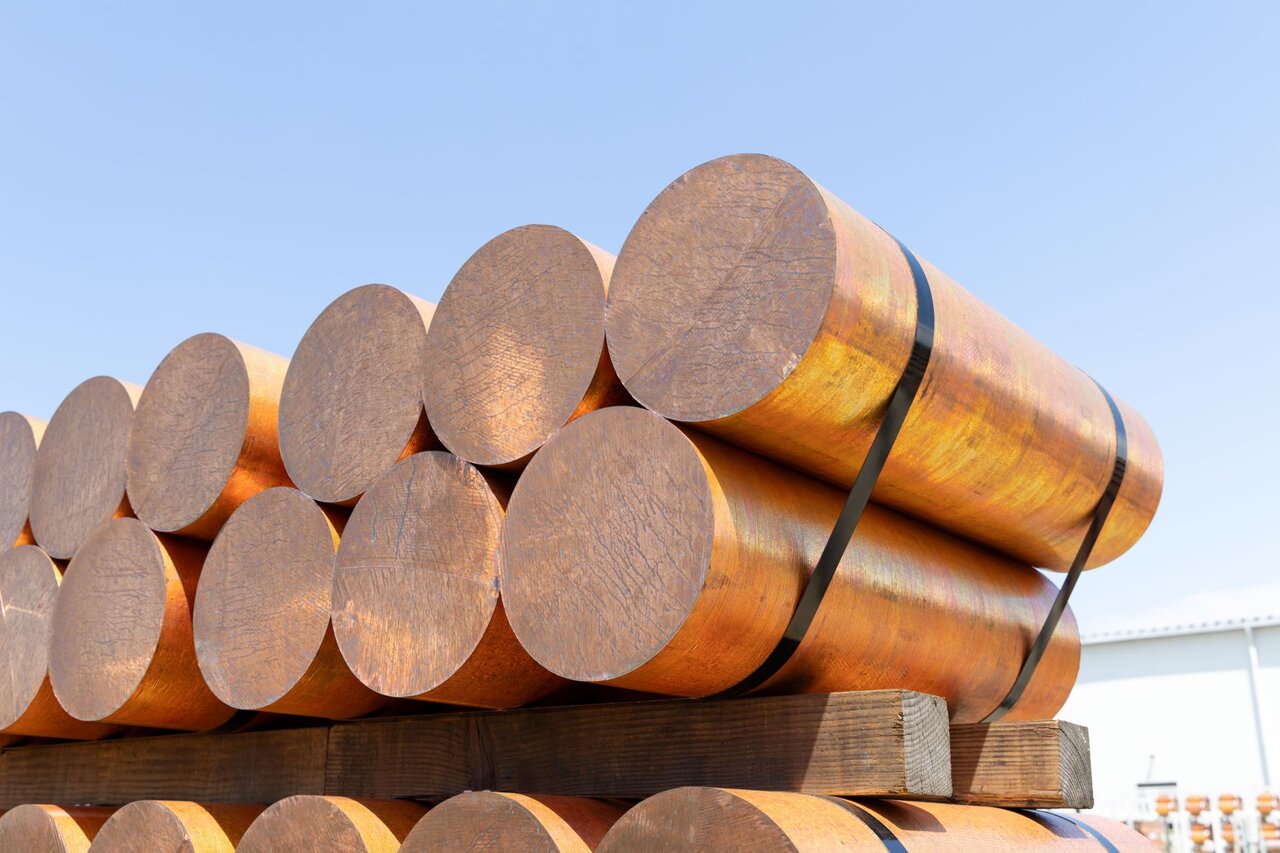
Meeting social expectations by tackling the work in front of us
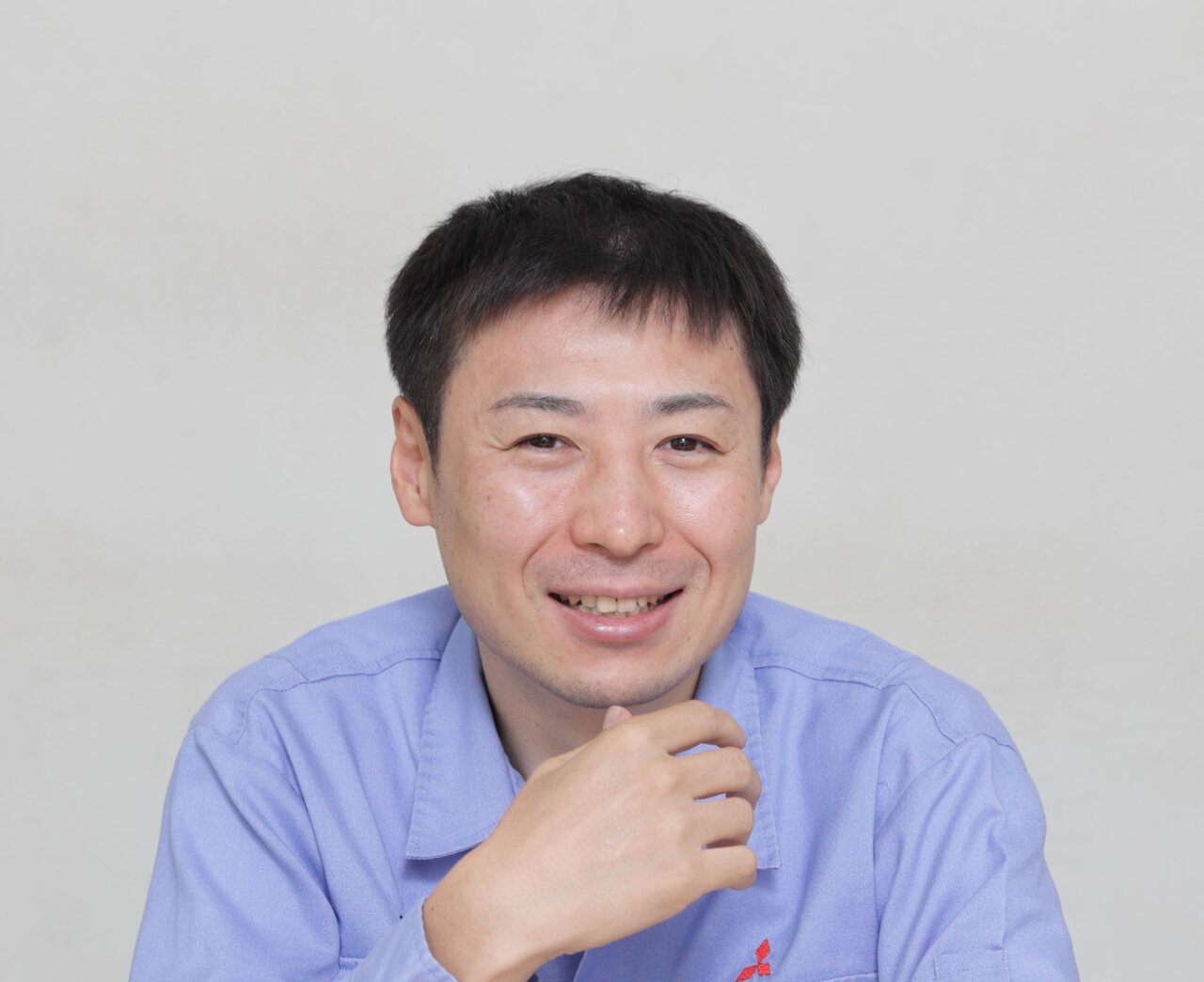
Tamakawa
From everyone’s remarks, I sensed a strong passion to work earnestly and contribute to society. Personally, I aim to first continue expanding sales of copper alloys to drive our sales growth. Our policy in the Production Engineering Sect. is to pursue safe and functional facilities and environments, high-quality products, and equipment and technologies optimized for low-cost production. I am dedicated to achieving these goals.
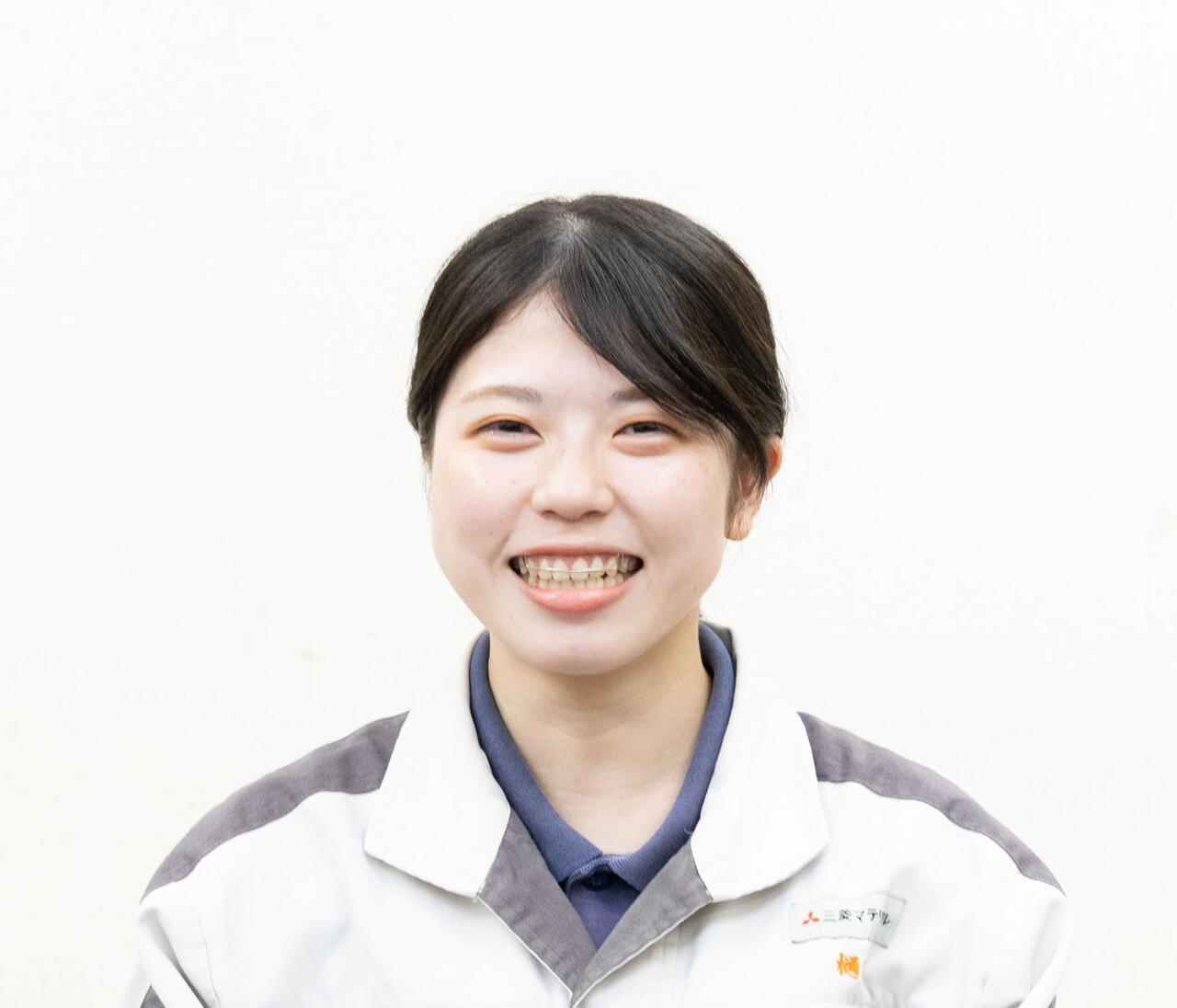
Higuchi
As part of the Sales & Production Control Sect., I will strengthen our collaboration with relevant parties to maximize the copper recycling rate and expand the use of alloy scraps by ensuring the smooth delivery of products and raw materials.
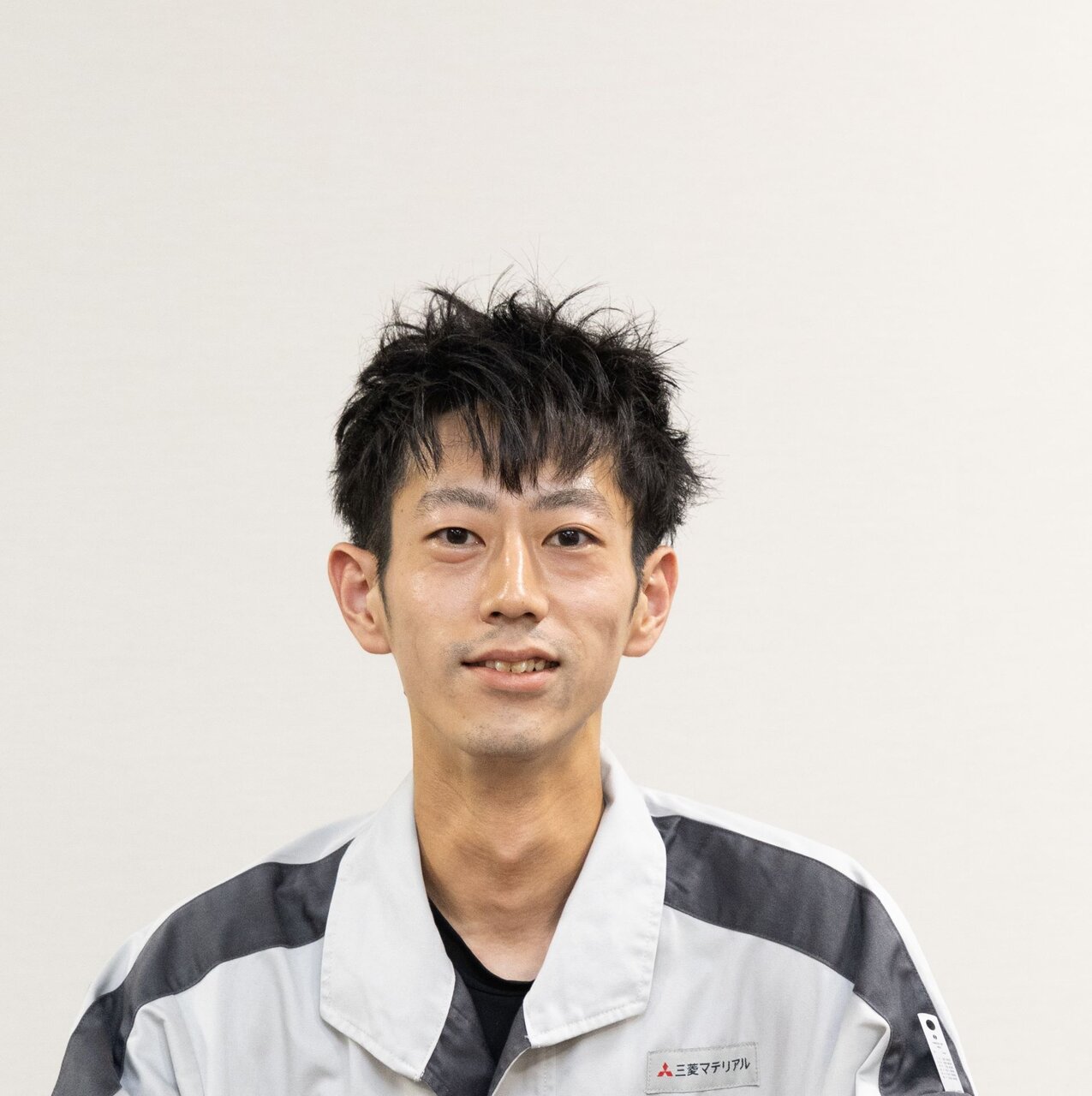
Fujita
The Sambo Plant’s plate products account for over 80% of the domestic market and also hold a significant share globally, embodying our status as the Global First Supplier. By diligently working to reduce defects, I aim to meet social expectations.
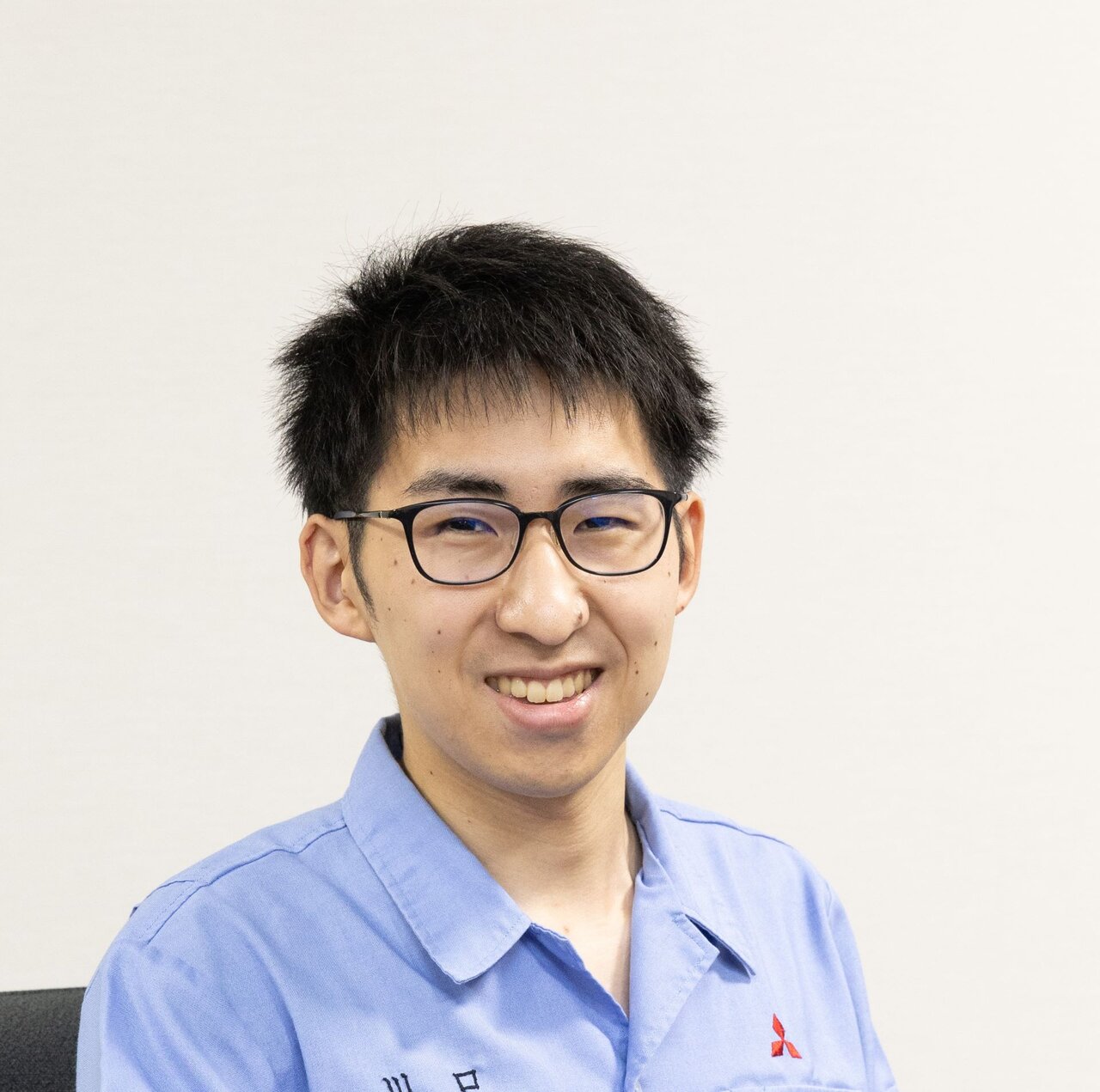
Kawaguchi
After hearing insights from across the company, I once again realized that every site is aligned in the same direction. I recognized that the items I handle are also important in another departments, which reaffirmed that we are on the right path.
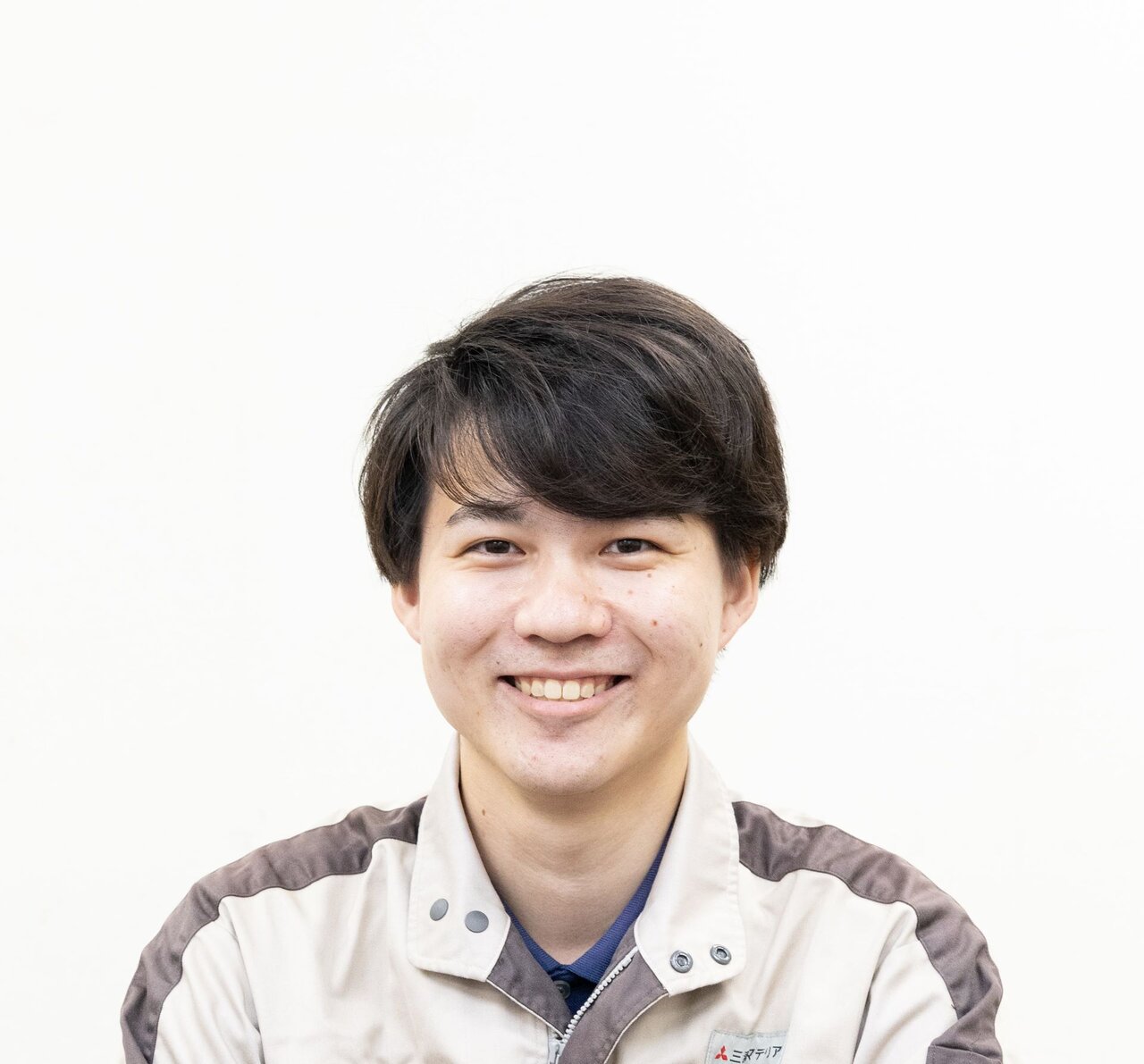
Takano
Collaborations across departmental boundaries are gradually strengthening, and I believe these collaborations are key to our survival. I have come to appreciate the importance of collaboration among all departments.
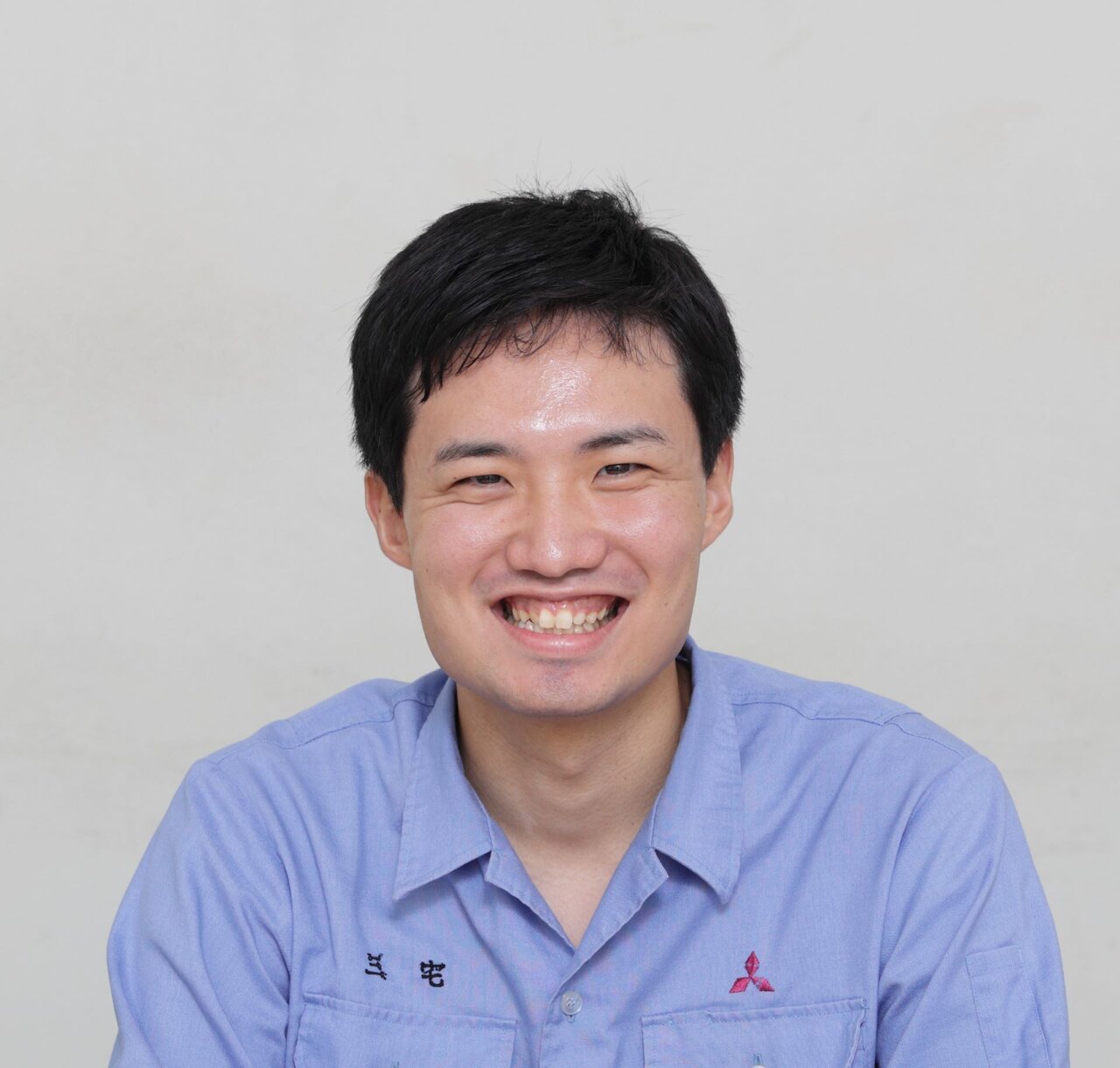
Miyake
Rather than collaborating only when an issue arises, we should encourage more people to learn about the operations of various departments at an earlier stage to foster collaboration. This will allow us to harness our potential. One of our company’s strengths lies in our ability to support all processes, from upstream to downstream. To leverage this strength, it is important to increase interaction.
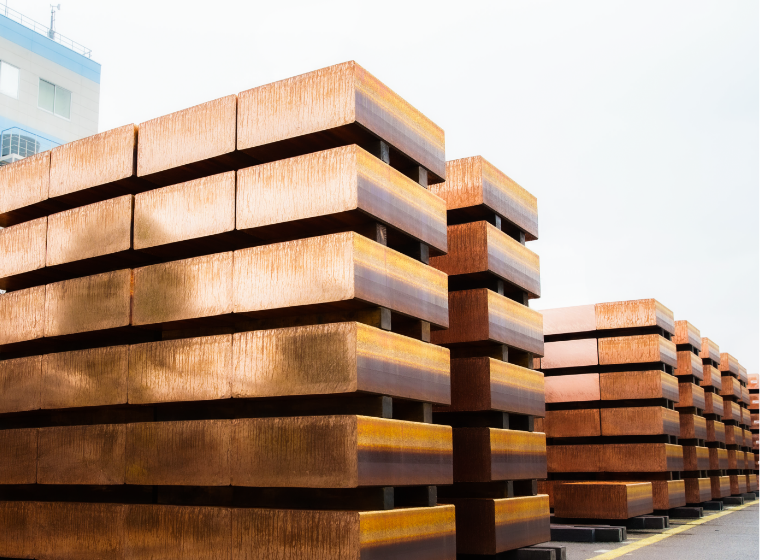
The six members who participated in the roundtable discussion shared their passion for the future and the challenges they want to take on.
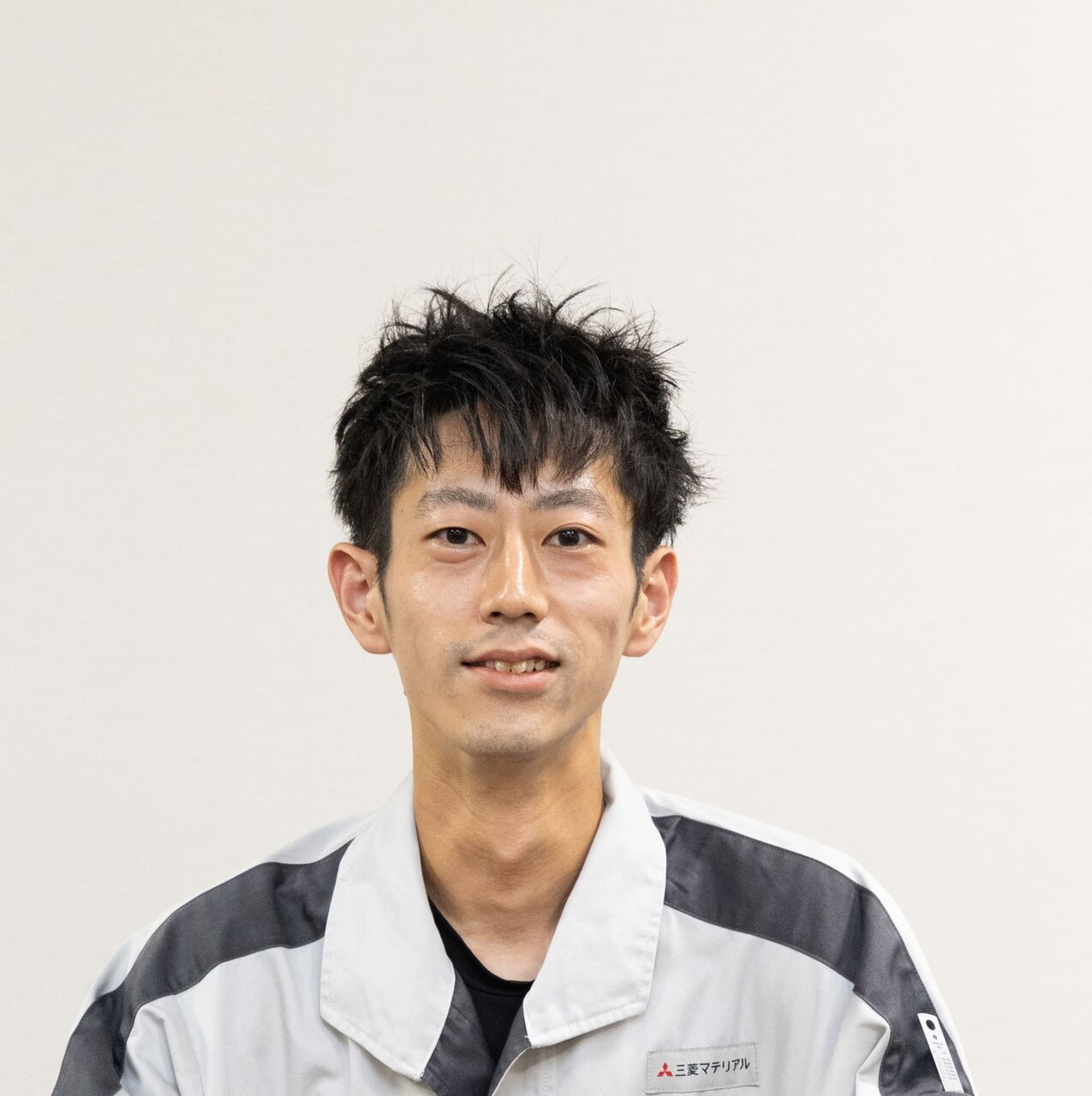
Sambo Plant
Kentaro Fujita
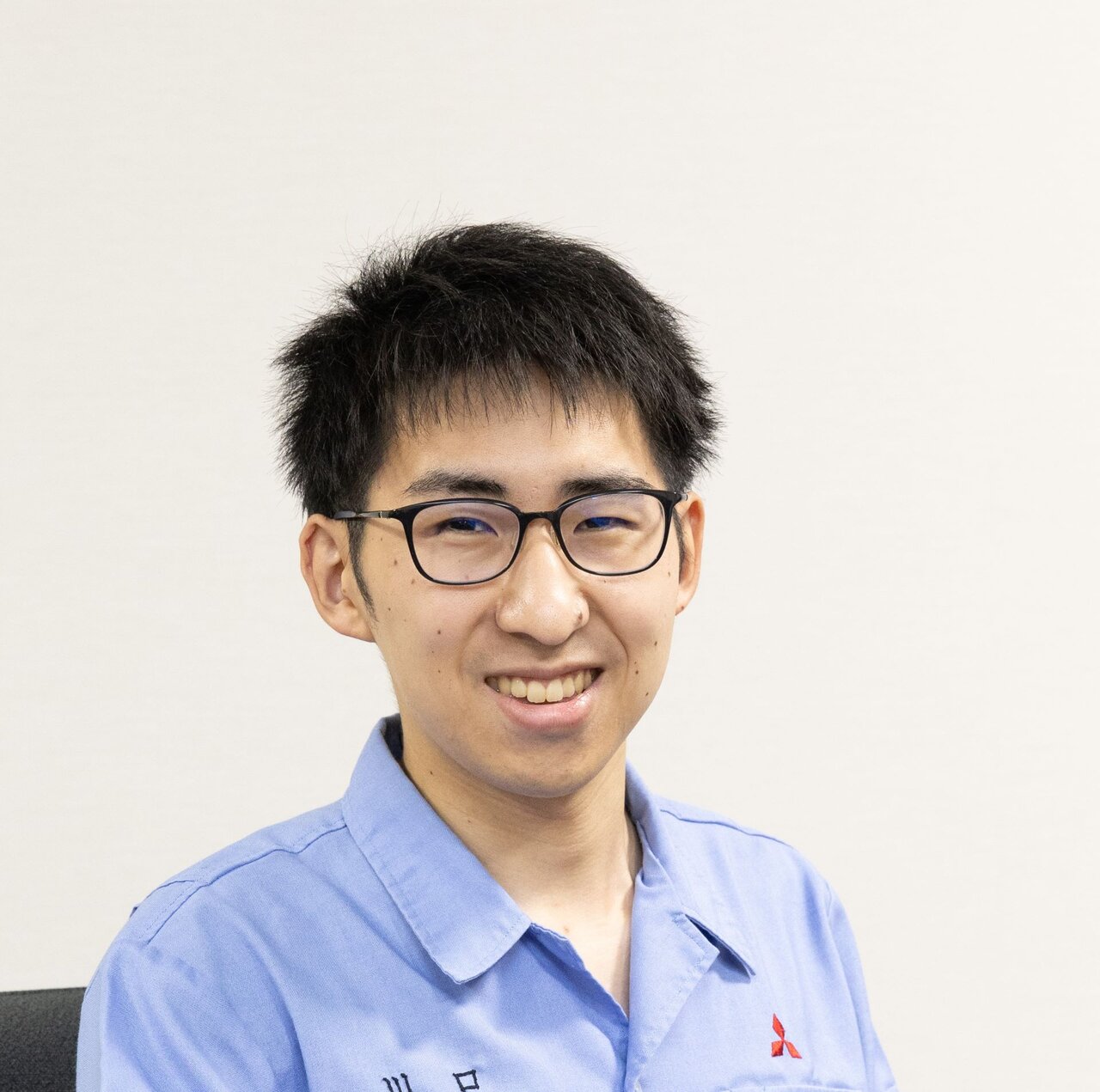
Technology & Development Dept.
Takuya Kawaguchi
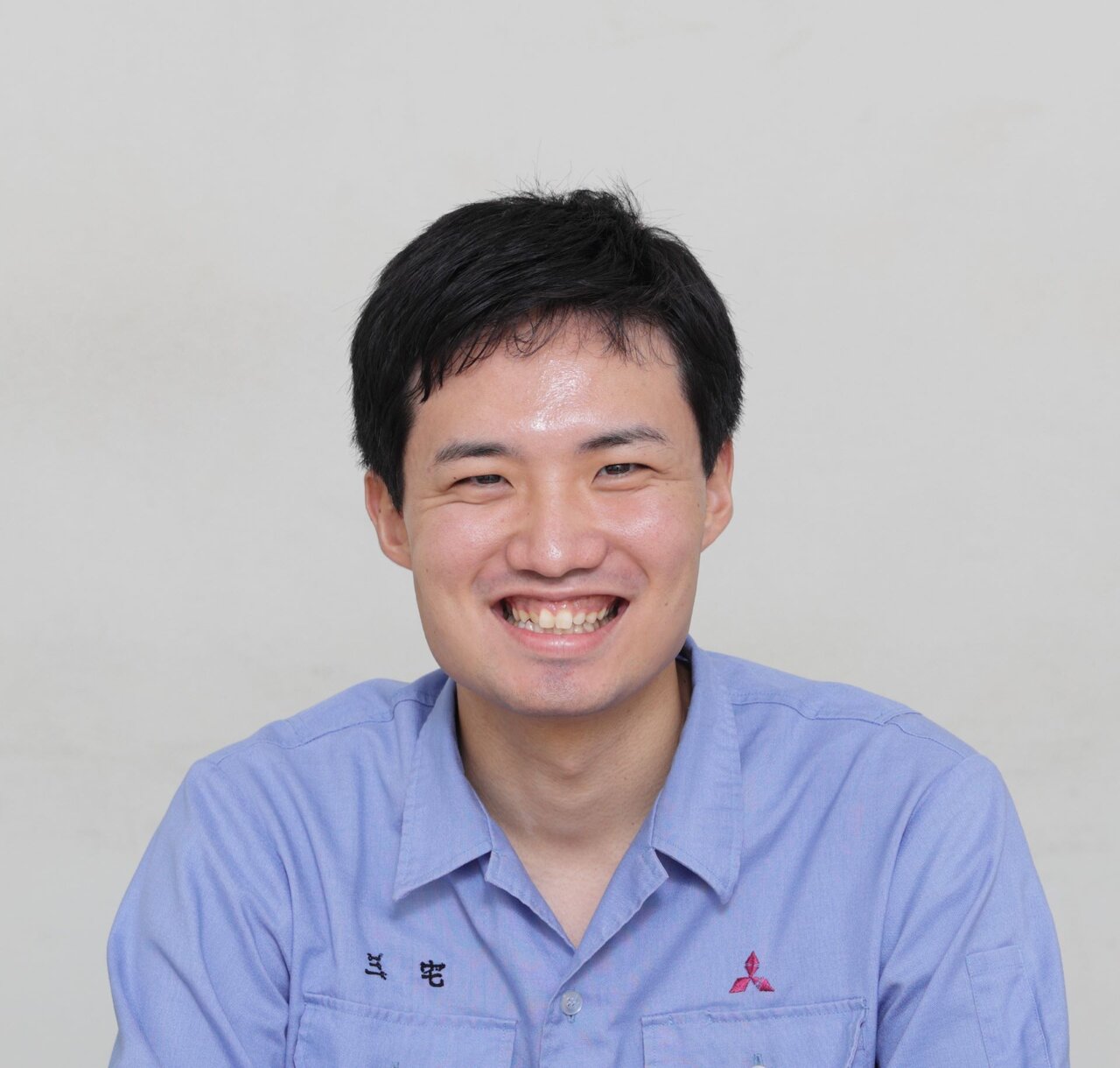
Wakamatsu Plant
Fuga Miyake
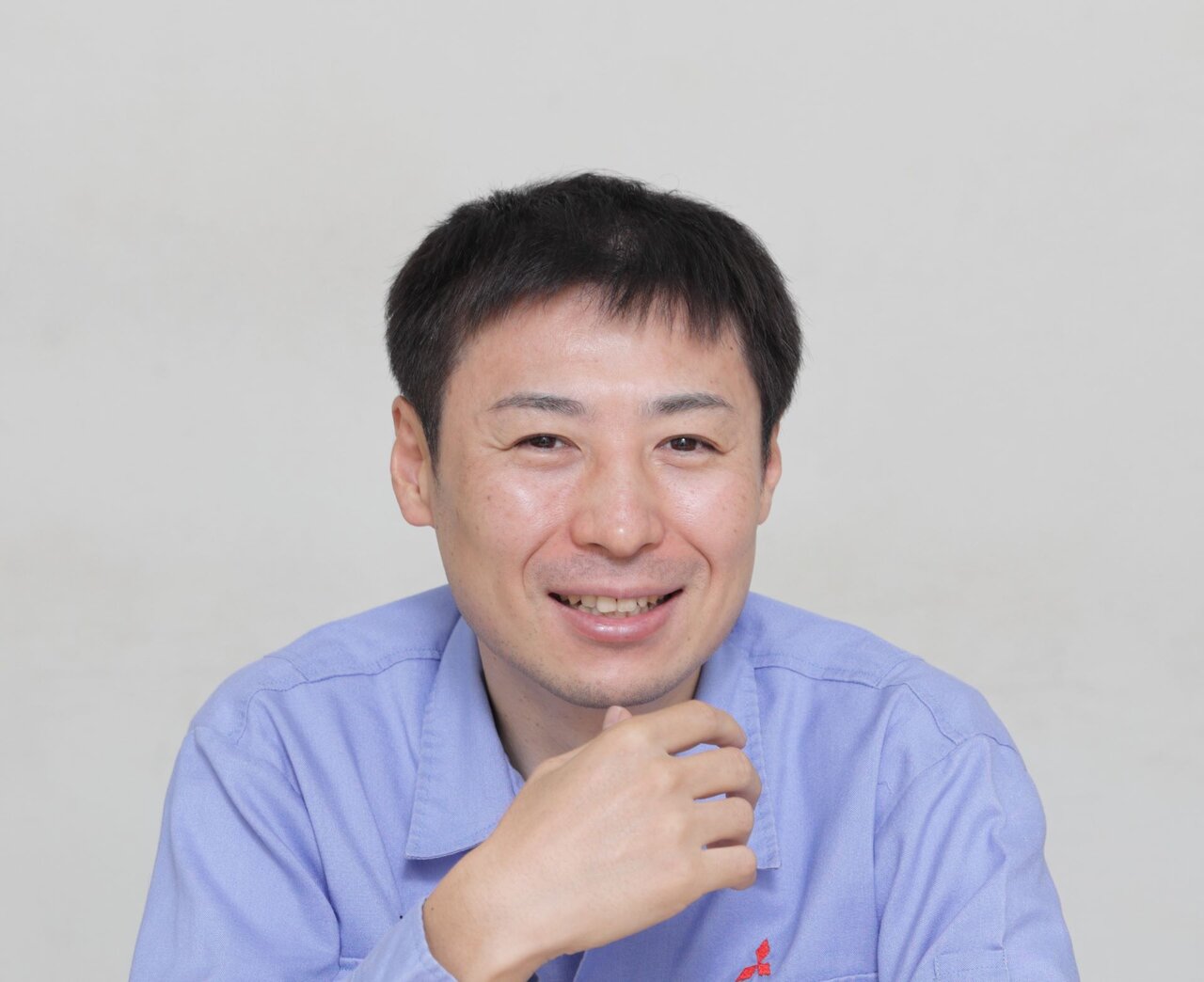
Wakamatsu Plant
Takashi Tamakawa
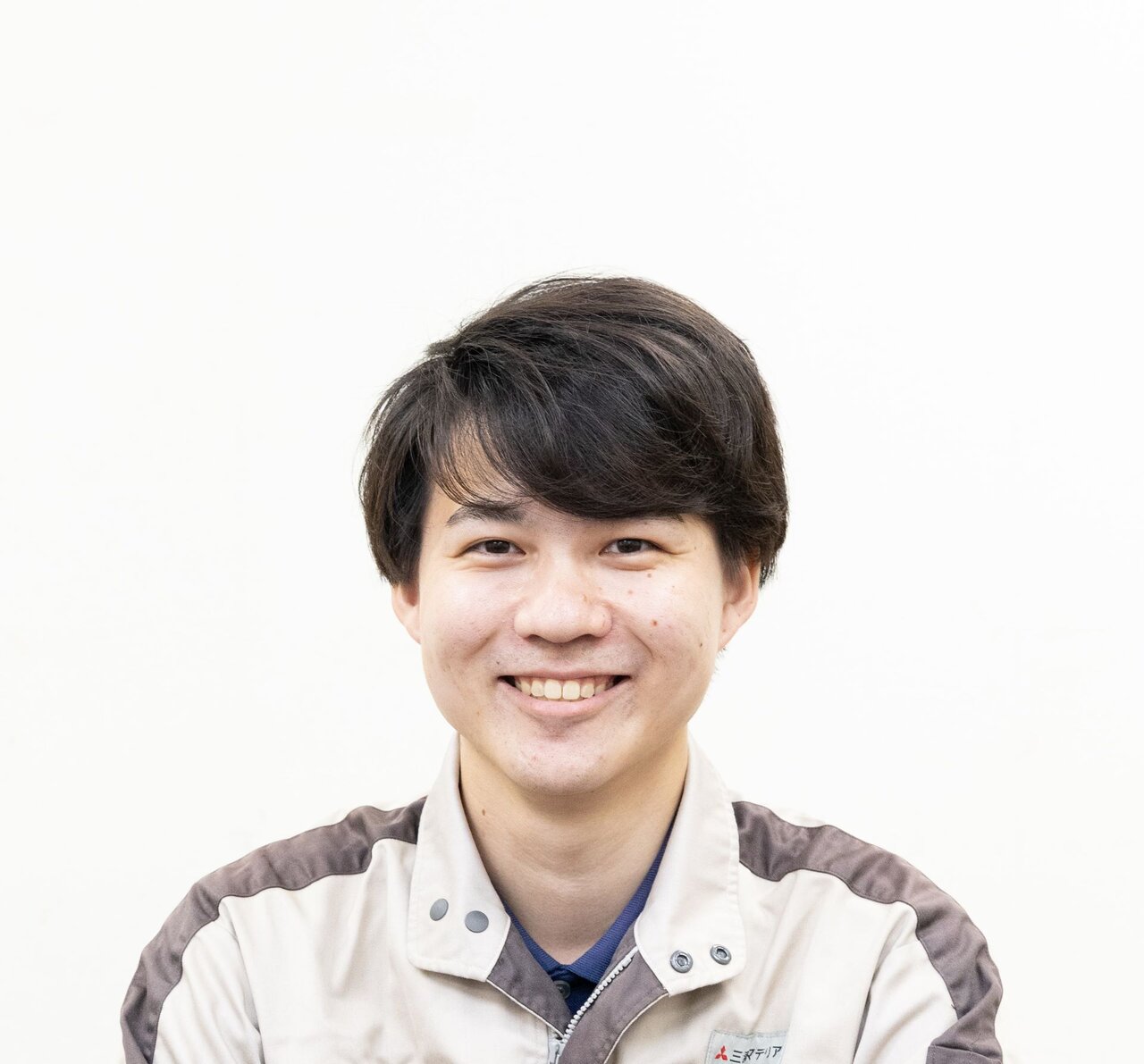
Sakai Plant
Akihiro Takano
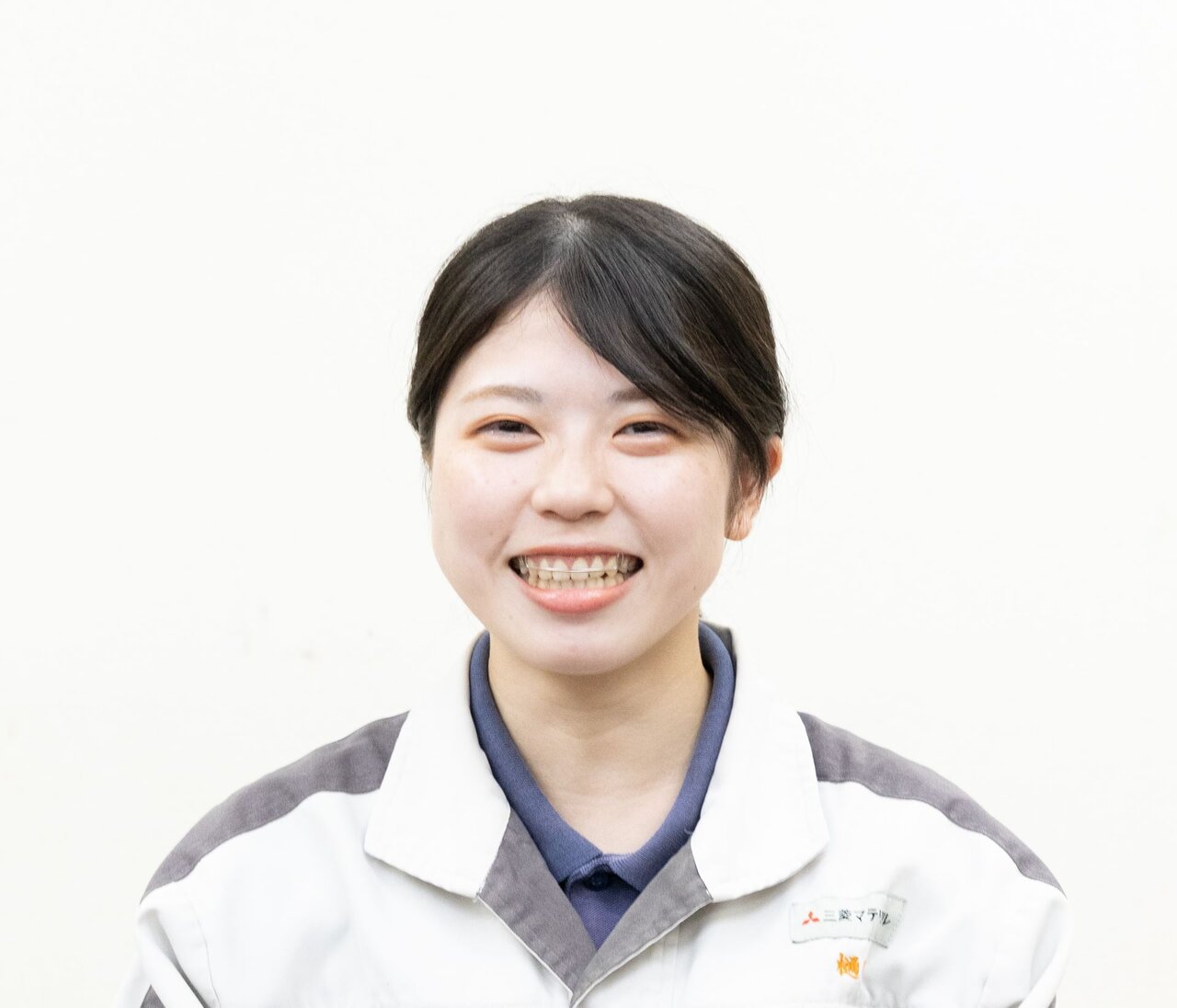
Sakai Plant
Mako Higuchi